Why You Should Think Twice Before Using PDMS in Microfluidic
What Is PDMS in Microfluidics?
PDMS (Polydimethylsiloxane) is a silicone-based polymer widely used in microfluidic chip fabrication. Its popularity stems from its optical clarity, biocompatibility, and ease of prototyping using soft lithography. For years, PDMS has been the standard in academic microfluidics labs around the world.
But is it still the best choice?
While PDMS microfluidic devices are easy to produce in small quantities, this material shows critical limitations for industrial, clinical, and even biological applications.
In this article, we’ll explore:
The main drawbacks of PDMS in microfluidics
Why PDMS may distort your experimental results
A new alternative: Flexdym, a next-gen elastomer for microfluidics
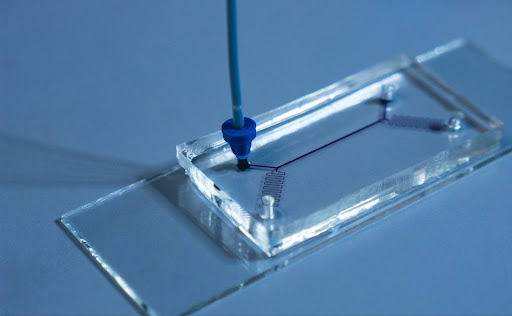
The Limitations of PDMS Microfluidic Devices
PDMS Absorbs Small Molecules
PDMS is highly permeable and tends to absorb hydrophobic molecules, such as drugs, hormones, dyes (e.g., Rhodamine B), and solvents.
This leads to loss of analytes, signal dampening, and inaccurate results.
It’s especially problematic for quantitative assays, drug screening, or single-cell analysis.
Toepke & Beebe (2006) showed that over 90% of Rhodamine B was absorbed into PDMS within 24 hours.
PDMS Is Not Scalable for Industrial Use
Producing PDMS microfluidic chips involves manual and time-consuming steps:
Mixing and pouring
Degassing
Curing
Cutting and bonding
These steps are prone to batch variability and human error. They are not suitable for mass production.
Berthier et al. (2012) concluded that “PDMS is not suitable for high-throughput or mass production.”
Unstable Surface Treatments
After plasma treatment, PDMS becomes temporarily hydrophilic—but only for a few hours. This leads to:
Poor cell adhesion
Instability in droplet microfluidics
Inconsistent capillary flow
This hydrophobic recovery undermines surface functionalization and long-term reliability.
Bonding Limitations and Time-Consuming Microfabrication
PDMS becomes hydrophilic after plasma treatment, but only temporarily. Within hours, its surface returns to being hydrophobic. This leads to:
Poor cell adhesion
Droplet instability
Unreliable capillary flow
Surface functionalization becomes unpredictable, especially in long-term experiments.
Oligomer Leaching Contaminates Experiments
PDMS is not fully crosslinked. Over time, unreacted silicone oligomers leach into the surrounding medium.
Consequences:
Cell toxicity
Altered gene expression
Interference with fluorescence-based assays
Regehr et al. (2009) showed that PDMS oligomers leached into media and altered gene expression in cultured cells.
Introducing Flexdym: A Better Alternative to PDMS
Flexdym vs PDMS: The Future of Microfluidic Chip Fabrication
Feature | PDMS | Flexdym |
---|---|---|
Small Molecule Absorption | High | Minimal |
Scalability | Low | High |
Surface Stability | Unstable | Stable |
Bonding | Challenging | Easy |
Reproducibility | Poor | Excellent |
Where Flexdym Excels in Microfluidics
Organ-on-a-chip
Wearable Devices
Diagnostics (e.g. Lateral Flow, Point-of-Care)
Cell culture and tissue engineering
- Multi-layer devices
PDMS vs Flexdym in the Lab and Beyond
With hot embossing systems like SUBLYM, Flexdym can be rapidly molded into complex microfluidic chips without cleanroom steps. Flexdym chips are reusable, reproducible, and scalable from R&D to production bridging the gap Polydimethylsiloxane never could.
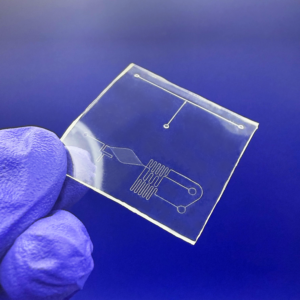
Ready to Move Beyond PDMS?
Stop struggling with the limitations of PDMS. Try Flexdym and design high-quality, scalable microfluidic chips without cleanroom requirements.
References
Want to Try Flexdym?
Get your Flexdym starter kit, access our free design tool FLUI’DEVICE, or ask for a demo. Stop prototyping in a dead-end , switch to Flexdym and build the future of microfluidics.
FAQ: PDMS Microfluidic
Is PDMS biocompatible?
Yes, but oligomer leaching and molecule absorption can compromise biological studies.
Why is PDMS not scalable?
Its manual fabrication process is too slow and inconsistent for large-scale production.
What’s better than PDMS?
Flexdym, a scalable, transparent, and biocompatible elastomer, designed for both research and industry.