Optimizing Microfluidics: The Advantages of Piercing Inlets and Outlets Directly During Fast Flexdym Moulding
Microfluidic devices have become indispensable in a variety of fields, from medical diagnostics to chemical synthesis. The demand for more efficient, precise, and scalable manufacturing processes has driven innovation in the way these devices are produced. This recent report outlines a breakthrough approach that integrates the piercing of inlets and outlets directly during the moulding process of Flexdym. Traditionally, the creation of inlets and outlets for these devices has required manual intervention, such as using metal hole punch pliers to create necessary holes after the device is moulded. However, this novel technique streamlines this process by integrating the piercing of inlets and outlets directly into the mold design, offering several significant advantages.
Optimizing Microfluidics Integrated Inlet/Outlet Piercing: Precision and Efficiency Combined
Traditionally, the creation of inlets and outlets in microfluidic devices has required manual intervention, typically involving metal hole punch pliers. This post-moulding step can be labor-intensive, time-consuming, and prone to inconsistencies. However, the new technique described in this blog revolutionizes this process by embedding the piercing directly into the mold design. Here’s how this approach stands out:
Elimination of Manual Labor:
By integrating the piercing of inlets and outlets into the mold itself, the need for post-processing steps is removed entirely. This not only reduces the labor required but also speeds up the production process, allowing for quicker turnaround times and higher throughput.Enhanced Precision:
The mold in fig 1 shows flat cylinders as inlets and outlets all with different height. After several test (refer to table 1), the optimal height to ensure that inlets and outlets are pierced cleanly and consistently turned to be 1.2 mm (fig 1). This level of precision is crucial for maintaining the integrity of microfluidic channels, preventing issues like leaks and ensuring reliable device performance.
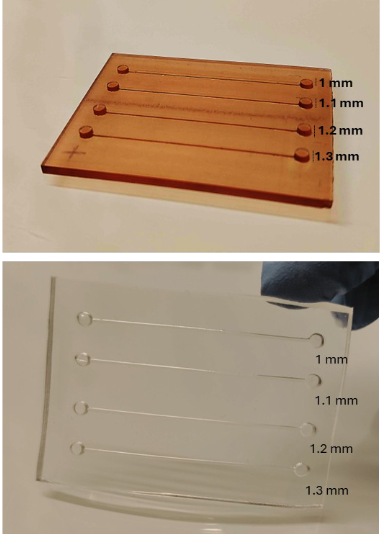
Fig1: 3D printed mold by SLA printer and the moulded Flexdym chip
Channel dimensions: wXh (mm) | Inlet and outlet shape | Inlet and outlet height (mm) | Spacer (mm) | Results |
1×0,5 | Pyramidal | 2,5 | 7 | Mould broken |
1,5×0,75 | Pyramidal | 3,75 | 11 | Mould broken |
1,5×0,75 | Pyramidal | 3,75 | 8 | Mould broken |
2×1 | Pyramidal | 5 | 8 | Mould broken |
0,5×0,5 | Pyramidal | 2,5 | 7,5 | Mould broken |
1×0,5 | Pyramidal | 2,5 | 7,5 | Mould broken |
1×0,5 | Flat cylinder | 1 | 7 | Not pierced |
1×0,5 | Flat cylinder | 1,2 | 7 | Not pierced |
1×0,5 | Flat cylinder | 1 | 6 | Not pierced |
1×0,5 | Flat cylinder | 1,2 | 6 | Not pierced |
1×0,5 | Flat cylinder | 1 | 5 | Not pierced |
1×0,5 | Flat cylinder | 1,2 | 5 | Not pierced |
1×0,5 | Flat cylinder | 0,9 | 5 | Not pierced |
1×0,5 | Flat cylinder | 1 | 5 | Not pierced |
1×0,5 | Flat cylinder | 1,1 | 5 | Not pierced |
1×0,5 | Flat cylinder | 1,2 | 5 | Not pierced |
1×0,5 | Flat cylinder | 1,3 | 5 | Pierced |
1×0,5 | Flat cylinder | 1,4 | 5 | Pierced |
1×0,5 | Flat cylinder | 0,9 | 5 | Not pierced |
1×0,5 | Flat cylinder | 1 | 5 | Not pierced |
1×0,5 | Flat cylinder | 1,1 | 5 | Not pierced |
1×0,5 | Flat cylinder | 1,2 | 5 | Not pierced |
1×0,5 | Flat cylinder | 1,3 | 5 | Pierced |
1×0,5 | Flat cylinder | 1,4 | 5 | Pierced |
3. Streamlined Workflow and Scalability:
Incorporating the piercing of inlets and outlets directly into the moulding process streamlines the overall workflow, making it easier to scale up production. For industries where large quantities of microfluidic devices are needed, this technique offers a clear path to more efficient and scalable manufacturing. The reduction in post-processing steps not only speeds up production but also simplifies the training required for operators, further enhancing scalability.
Optimizing Microfluidics, Fast Flexdym moulding: Accelerating Production Without Compromise
In addition to the innovative piercing technique, the report also details a highly efficient Flexdym moulding process that further enhances production speed. The parameters used in this process— 180 seconds at 165°C with 5 mm spacers—result in a quick and reliable moulding cycle that doesn’t sacrifice quality for speed. Why this fast moulding process is a game-changer?
- Significantly Reduced Production Time: The ability to mould Flexdym in less than 3 minutes allows for rapid prototyping and large-scale production runs. This speed is critical in industries where time-to-market can be a competitive advantage, such as in the development of diagnostic devices or lab-on-a-chip technologies.
- Improved Bonding and Device Integrity: Despite the accelerated pace, the moulding process yields high-quality results, with strong, clear bonds and precise channel dimensions (fig 2). Even under microfluidic testing at flow rates up to 900 μL/min, the thermal bonds remain secure, demonstrating the technique’s effectiveness in producing robust, leak-proof devices.
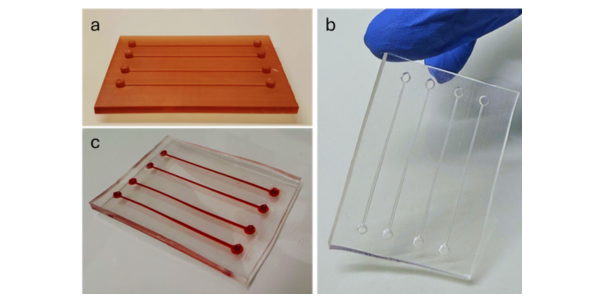
Fig2: a) mould with 4 hole with inlet height of 1.5mm; b) Flexdym chip pierced using hot embossing for moulding and bonding; c) example of fluidic experiments
Conclusion
The combination of integrated inlet/outlet piercing and fast Flexdym moulding represents a significant leap forward in microfluidic device manufacturing. By eliminating manual post-processing steps, enhancing precision, and accelerating the moulding process, this dual innovation addresses challenges in laboratory and industry. The result is a more efficient, cost-effective, and scalable production method that doesn’t just keep pace with the demands of modern microfluidics—it sets a new standard. As the field continues to evolve, these advancements will be pivotal in enabling the next generation of microfluidic devices, driving progress in medical diagnostics, environmental monitoring, and beyond.