Room Temperature and Equipment-Free Microfluidic Device assembly & Bonding - Application Note
Introduction
The fabrication of microfluidic devices, essential for numerous applications in biomedical, pharmaceutical, and chemical industries, faces significant challenges, primarily related to bonding. Ensuring robust, and reliable bonding without the need for expensive cleanroom facilities is crucial for the widespread adoption of microfluidic technology.
This application note focuses on the use of Flexdym™, a commercial soft thermoplastic elastomer, as an effective and versatile bonding material. It eliminates the need for expensive equipment and additional treatments. Thereby offering a high quality, cost-effective and time-saving alternative, for microfluidic device fabrication.
The microfluidic device designed and fabricate for testing the room temperature bonding performance, consist of alternating air and elliptical and circular flow channels with spacing (s) of either 10, 50, 100 or 200 µm (showed in fig1).
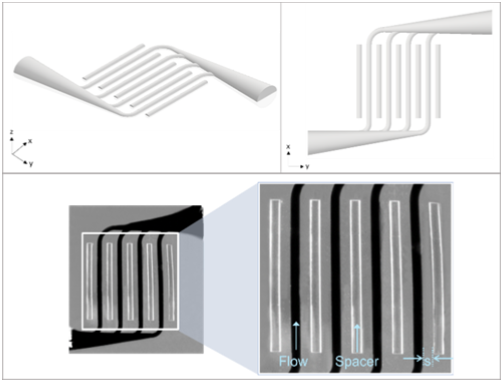
Fig1. Custom chip for microfluidic leak tests. Top: Autodesk Inventor view of the semi-elliptical channels design. Bottom: optical image of a chip with dyed-water in the flow channels. The chip shown here has s = 200µm.
Flexdym™: A Versatile Bonding Material
Flexdym™ is a styrene-ethylene-butylene-styrene (SEBS) based copolymer. It combines the desirable properties of both thermoplastics and elastomers. It can be molded when heated, and retains its form after cooling, making it suitable for microfluidic applications. Flexdym™ is optically transparent, flexible, and has a comparable Young’s Modulus to PDMS (Polydimethylsiloxane).
Recently commercialized, Flexdym has demonstrated its advanced key benefits within more than 20 peer-reviewed. Indeed, it has been shown that the use of a commercial SEBS thermoplastic elastomer (TPE) as tailored and excellent material solution for applications in the microfluidic domain. In particular, in contrast to the bonding of thermoplastic materials. Which is commonly achieved by a combination of pressure (to maintain surfaces in contact) and thermal activation (to generate inter-diffusion and reorientation of polymer chains), SEBS soft blocks promote effective bonding properties at ambient conditions.
SEBS materials and some of its derivates are included in many pressure-sensitive adhesives. Such as the famous Post-it sticker, which can easily be glued to a broad range of solid supports, without mediation by heat, elevated pressure, or solvents.
Fig. 2 represents a unique and convenient demonstration of a hybrid, thermoplastic microfluidic device. Realized without heating or applied pressure. It is worth noticing that embedded microchannels do not show any signs of deformation. SEBS therefore, is suitable for assembly and bonding of thermoplastic-based micro-fluidic networks. Without the need for sophisticated equipment or surface treatment processes.
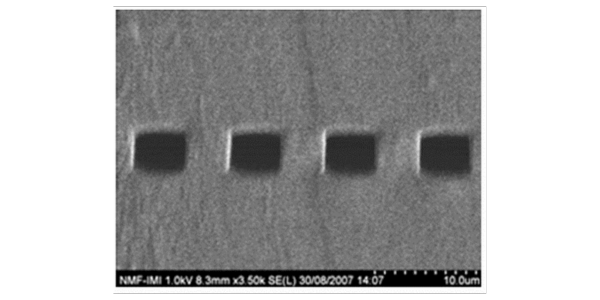
Fig2. Cross-sectional view of embedded microchannels (4.2 and 5 µm in depth and width, respectively) obtained by bonding of an SEBS micro-fluidic networks to a Zeonor substrate
Furthermore, the slow adhesive property of Flexdym is particularly advantageous. It provides time for precise alignment and adjustment during assembly, reducing the risk of errors and ensuring high-quality bonds. Additionally, the strong affinity of Flexdym to itself enhances the durability and robustness of these bonds, making Flexdym an ideal material. Not only as a substrate but also as a sealing solution in microfluidic device fabrication. Its ability to bond at room temperature ensures the preservation of structures and dimensional stability.
Likewise, the Pressure Sensitive Adhesive (PSA) properties of Flexdym make it an outstanding material for a wide range of applications, particularly in microfluidics. Its self-adhesive, self-stick nature allows for straightforward and efficient bonding, without the need for additional complex processes. Simplifying the assembly of microfluidic devices and ensuring consistent and reliable seals, crucial for maintaining the integrity of the microchannels.
Fundamental benefits of the room temperature bonding (RTB)
Room temperature bonding of Flexdym offers several fundamental benefits, particularly in terms of bonding quality, structural integrity, and advanced suitability for biological applications. More in details below are described the major benefits of the RTB.
Preservation of Sensitive Structures and Avoidance of Thermal Stress: RTB avoids the risk of deforming, warping, or damaging materials. Making it ideal for microfluidic and nanofluidic devices fabrication, with intricate patterns and structures. Since no heat is applied, there’s no differential expansion or contraction of materials during the bonding procedure. This prevents mechanical stress, cracks, or misalignments in multi-layered structures (refer also to Fig2).
Usually, thermal expansion or contraction leads to a change in the dimensions of the microchannels, and so as a consequence, to a change in terms of shear stress or pressure drop in the microfluidic device. As an example, if we consider a channel of 1mm length and a width of 100 µm, the shear stress increases 78% when the channel height decreases from 12 µm to 9 µm. Also, the pressure drop increases of 137% over the same height change.
This gives a clear picture that as the channel narrows, as a consequence of the bonding procedure, the shear stress and pressure significantly increase. Which has important implications for fluid dynamics in microfluidic systems. Conclude there, robust and reliable dimensional integration are key to ensure both high research and development activities (reliable results, clinical trials, productions development).
Biological Compatibility:
Room temperature bonding is particularly advantageous in biological settings, where sensitive biomolecules, cells, or tissues can be damaged by heat. By preserving the biological integrity of samples and avoiding the risk of denaturation, Flexdym bonded at room temperature is highly compatible with diagnostic, therapeutic, and lab-on-chip systems used in life sciences.
This process not only preserves the material’s properties, but it also facilitates surface modifications, such as functionalization with biomolecules or cell-adhesion coatings, enhancing its compatibility for biological environments. These modifications also make Flexdym ideal for advanced applications like tissue engineering and biosensing. Additionally, unlike solvent bonding, RTB does not introduce chemicals or solvents that could contaminate the biological samples. This reduces the risk of unwanted reactions or contamination that can harm cells or affect experimental results. Since RTB can be conducted without the need for heat or solvents, it’s easier to maintain sterile conditions, which is crucial for bio-application.
Room Temperature Bonding plays a key role in the bio-integration of microfluidic devices. Bio-integration refers to the successful incorporation of biological components into a device while preserving their functionality and viability. Thanks to Flexdym self-adhesive and self-sticking properties, biological samples like antibodies or peptides can be integrated into the microfluidic compartment before the bonding process.
Flexdym can then be bonded to the most suitable substrate for the experiment at room temperature, preserving the biomaterials, by maintaining their structural integrity and function. Unlike solvent bonding, RTB avoids introducing chemicals or solvents that could contaminate biological samples. Minimizing the risk of harmful reactions or contamination, that could affect cells or experimental outcomes. Additionally, since RTB does not require heat or solvents, it helps maintain sterile conditions, which is essential for bio-integration.
Faster Processing and Simplicity:
Without the need for heating, cooling, or drying phases, RTB simplifies the bonding process. This can lead to faster production times and reduced equipment costs, improving manufacturing efficiency. Indeed, simplified the prototyping process allow for rapid iteration and modification of designs. This flexibility is particularly valuable in research and development settings, where designs may need to be quickly adjusted. Moreover, room temperature bonding doesn’t involve solvents, as for chemical bonding. Reducing the risk of contamination and the need for additional processing to remove solvent residues.
No Need for Equipment or Surface Treatments:
As mentioned, one of the most significant advantages of Flexdym™ is its ability to bond at room temperature with various substrates. Without the need for plasma treatment, thermal bonding, or any specialized equipment. This capability is particularly beneficial when an optimized bonding procedure, depending on the design and application of the device, might be challenging to address. Flexdym™ demonstrates strong bonding at room temperature with substrates such as Flexdym, COC (Cyclic Olefin Copolymer), PS (Polystyrene), and even PMMA, without requiring any pre-treatment.
Cost and Time Savings:
the ability to achieve effective bonding without additional treatments or equipment translates into substantial cost and time savings. Traditional bonding methods often involve the use of plasma machines, thermal bonding setups, or adhesive materials. All of which contribute to increased costs and complexity. Indeed, the bonding process influences the total cost of the microfabrication process by a factor of 3 compared to the other steps involved in the fabrication process. By using Flexdym™, the costs are significantly reduced, making microfluidic device fabrication more accessible to researchers and industry professionals alike.
Material Compatibility:
Many polymers and heat-sensitive materials can be bonded without risk of thermal damage. RTB ensures a broader range of materials can be used without worrying about thermal expansion or degradation.
Scalability:
RTB processes can be easily scaled up without the complexity of thermal management systems. This is beneficial for high-volume production of devices like microfluidic chips, where delicate features need precise bonding. Both laser and ultrasonic welding are well-established techniques for scaling up fabrication processes at the microscale level. However, when bonding microfluidic chips, both techniques suffer from several drawbacks.
For example, laser welding uses concentrated heat, which can cause localized thermal stress, and this can deform or damage delicate microfluidic channels, affecting the chip’s precision. Additionally, the surfaces to be bonded often need to be flat and absorbent, which can add complexity to the preparation process. It also may not work well with multi-material microfluidic chips, limiting design flexibility.
On the other hand, ultrasonic welding often requires significant pressure to ensure a strong bond. This can lead to deformation of thin or fragile components in microfluidic chips. Moreover, the ultrasonic horn can wear out over time, leading to inconsistent weld quality, especially in high-precision applications. Ultimately, both laser and ultrasonic welding are fast, energy-efficient, and widely used in industrial applications. However, they pose challenges for bonding microfluidic chips, which often contain sensitive, small-scale features requiring precise and careful bonding methods.
Bonding Performance:
Flexdym™ exhibits outstanding bonding performance across various substrates (ref Figure 3). Results have shown that it achieves strong and reliable bonds with PMMA, COC, and Flexdym™ itself, even when untreated. In particular, the best performance in terms of withstood pressure was obtained by Flexdym-COC bonding. The pressure achieved by Flexdym – Flexdym bonding, for this particular and complex design, was around 600 mbar. Other studies have demonstrated that this type of bonding (Flexdym-Flexdym) can withstand pressures up to 2 bar for reversible bonding. Up to 3 bar for permanent bonding (see Salmon et al. or Roy et al).
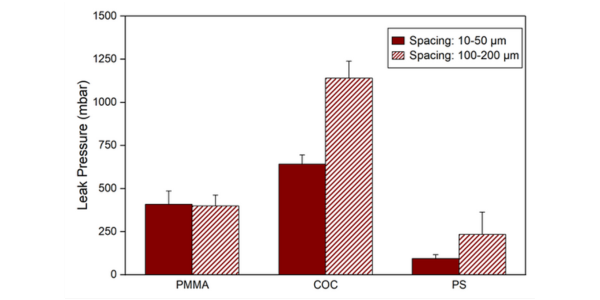
Fig3: Microfluidic leak test results. Bond strengths are shown as average leak pressures ± SEM.
Application Scenarios
Flexdym™ stands out as an ideal material for microfluidic device applications due to its high quality, cost-effectiveness, and ease of fabrication. Whether for prototyping, small-scale production, or industrial manufacturing, Flexdym™ ensures that quality remains uncompromised. While offering a seamless transition from research to market-ready products. Indeed, it bridges the gap between prototyping and industrial-scale production, making it a versatile solution for a wide range of microfluidic applications. In addition, its compatibility with injection molding allows for a smooth transition from R&D to full-scale manufacturing. Ensuring consistency and quality at every stage, and solidify its position as a leading material for microfluidic innovation fields.
Conclusion
Flexdym™ presents a unique opportunity to simplify the fabrication process of microfluidic devices, by keeping high quality performance. Its ability to bond effectively without additional treatments or equipment not only reduces costs but also accelerates the development timeline. Room temperature bonding presents a promising alternative, preserving structural integrity, improving energy efficiency, and providing a simpler, more environmentally friendly process, especially for sensitive applications.
Room temperature bonding of Flexdym also ensures the biocompatibility and suitability of the final device for biological applications, providing stability and consistency in device performance. These advantages make Flexdym a highly attractive material for microfluidic device fabrication. Especially in applications where high precision and reliability are critical.
Overall, the PSA properties of Flexdym contribute to its versatility, ease of use, and reliability, solidifying its position as a preferred material in advanced microfluidic applications and beyond. Flexdym™ is an attractive choice for both academic research and industrial applications in the microfluidics field. This application note demonstrates how Flexdym™ can significantly lower the barriers to entry in microfluidic device fabrication. Making this technology more accessible and practical for a broader range of applications.
References
1.“Investigating the bonding properties of polymers with different treatment parameters for facile and accessible microfluidic device fabrication”, by Calzuola et al.
2.“Facile engineering and interfacing of styrenic blockcopolymers devices for low-cost, multipurpose microfluidic applications”, by Salmon et al.
3.“Prototyping of microfluidic systems using a commercial thermoplastic elastomer”, by Roy et al.