Sublym Hot embossing + Bonding 2-in-1 machine
Application Note
Introduction
The evolution of the microfluidics field demands fabrication methods that are both efficient and cost-effective. The Sublym machine, which we can call a “2-in-1 machine”, facilitates the efficient hot embossing and bonding of advanced Flexdym materials with other classical thermoplastics (COC, PMMA, PS…), streamlining the fabrication process and ensuring reliable outcomes.
This application note highlights the use of Sublym for hot embossing microfluidic channels on Flexdym and subsequently bonding it with various thermoplastics, providing a comprehensive solution for microfluidic device fabrication.
Sublym: The 2-in-1 Machine
Sublym Hot embossing + Bonding machine, both integrated into a single, compact platform, streamlining microfluidic device fabrication by minimizing equipment requirements and process steps. Its design prioritizes compactness and precision, making it especially suitable for research labs and small-scale production environments where space is limited.
In contrast, systems like those from EVG and Obducat cater to broader applications, from R&D to high-volume industrial production. EVG focuses on industrial robustness and scalability, with systems optimized for high-throughput operations in semiconductor and MEMS production environments, which typically require larger footprints. Obducat offers flexible solutions that bridge R&D and production needs, with compact research options like the Sindre® series and larger, high-throughput systems like the Eitre® models to support industrial scalability. Both machines require larger and clean spaces, like a clean room environment.
These differences reflect distinct priorities: Sublym emphasizes precision in smaller, flexible setups ideal for limited-space environments with the possibility of integrating it in a simple fume hood, while EVG and Obducat address scalability and versatility for high-throughput production and diverse operational needs.
The following table show the different machine based on their application, size and price.
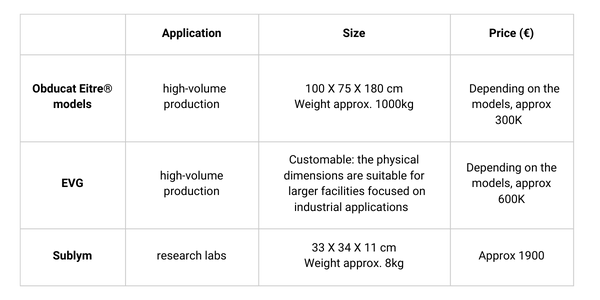
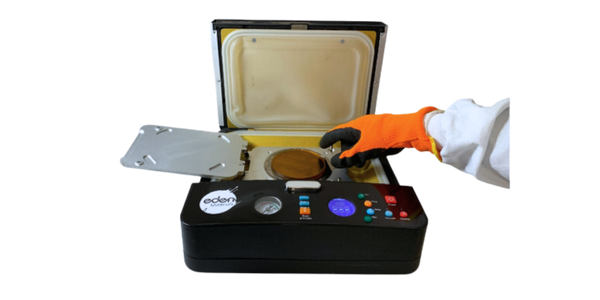
Fig1: Sublym
Flexdym™ and Its Advantages
As classical thermoplastics, Flexdym™ is a styrenic block copolymer that can be molded when heated and maintains its form upon cooling, Additionally, Flexdym™ is optically transparent, flexible, and has a Young’s modulus comparable to PDMS, making it suitable for applications requiring flexibility to enhanced conformable assembly and a key asset for enhanced bonding.
Advantages of Flexdym™
- Optical Transparency: Ensures clear visualization of fluid flow (Visible & Fluorescence)
- Intrinsic Adhesive Properties: Allows for low to medium bonding strengths without additional equipment or treatment. (0.5 to 2 bars, see figure 3)
- Flexibility and Ease of Processing: Ready to use, on-demand (no preparation), Flexdym™ demonstrates to be very easy to mold (0.5-5 min) and suitable for bonding with various thermoplastics, such as PMMA, COC and PS. Using thermal treatment significantly cuts the cost of the total process for microfluidic chip fabrication.
- Industrial Suitability: Ideal for both R&D and industrial fabrication due to its compatibility with injection molding techniques and roll-to-roll technology. Core value to process streamless this the same material interface at all stages of development saving month, year most probably.
Materials and Methods
Materials
- Flexdym™: for the fluidic channels
- Thermoplastics: Flexdym™, PMMA, COC and PS as substrates
Equipment
- Sublym Machine: A combined hot embossing and bonding system.
Process Overview
- Hot Embossing: The Sublym machine precisely patterns Flexdym™, as well as other thermoplastics like COC, PS and PMMA, by applying controlled heat and pressure.
- Thermal Bonding: The same machine is used to bond Flexdym™ to various thermoplastics, ensuring reliable results.
- Vacuum assistance: For homogeneous pressure (polymer transport) and avoid trapped air bubbles upon Molding & Bonding. Indeed, during the hot embossing process, maintaining consistent pressure across the substrate is crucial for the uniform distribution of polymer transport and filing. Vacuum assistance helps create this homogeneous pressure by eliminating variations caused by trapped air or uneven surface contact. Moreover, air bubbles trapped between the mold and the polymer during molding or bonding can lead to defects, such as incomplete patterns or weak bonds. By applying vacuum assistance, the Sublym machine removes air from the system, enabling a flawless interface between the polymer and the mold.
Experimental Setup
Hot Embossing Parameters
- Temperature: the melting temperature for Flexdym™ (between 110 – 160°C).
- Time: Adjusted to ensure complete pattern replication, usually less than 3 minutes.
Bonding Parameters
- Temperature: Specific to material combinations:
Flexdym™ – Flexdym™ (70°C).
- Flexdym™ – PMMA (80°C – grade: mcs-PMMA-08 – Tg:110°C)
- Flexdym™ – COC (80°C, grade: mcs-COC-13 – Tg: 142°C)
- Flexdym™ – PS (90°C, grade: mcs-PS-17 – Tg: 100°C)
Pressure/Vacuum: the one pre-settled by the Sublym (0.7 MPa) to ensure intimate contact between layers during bonding.
Hot embossing process of Flexdym™ & rigid thermoplastic (COC/PMMA)
The key steps for hot-embossing include:
- Preparation of the Master Mold: The microfluidic patterns are first designed and fabricated onto a rigid master mold, typically SU8 or epoxy, which can be fabricated starting from either SU8 mould or 2PP 3D printing mold.
Embossing: Flexdym™ or other thermoplastic, like PMMA, is placed over the master mold, heat and pressure are applied using the Sublym. The temperature is typically maintained between 110°C and 160°C.
The pressure/vacuum is the pre-settled one (ca 0.7 MPa). Pressure and heat allow the microfluidic patterns to be transferred accurately onto the Flexdym surface.Cooling and Demolding: After embossing, the system gradually cools the polymer chips stack outside the machine. This controlled quenching process ensures the microstructures retain their shape and integrity while avoiding thermal stresses. Indeed, the polymer’s inherent stickiness and compression set properties ensure precise pattern fidelity during external cooling without the need for external pressure to maintain the sandwich molded Flexdym™ and mould. The Flexdym™ is then carefully demolded, revealing the replicated microfluidic patterns (tip: IPA can be used to facilitate the demolding step).
Optimized parameters for Flexdym™ Embossing
Temperature: The embossing temperature should be finely controlled to avoid either incomplete pattern transfer (too low temperatures) or material degradation (excessively high temperatures). For our specific case, we used 120°C but Flexdym™ and other thermoplastics can hold much higher temperatures.
Pressure: Adequate pressure is essential to ensure that Flexdym™ conforms to the mold’s microstructures. A typical pressure is 0.7 MPa. This makes Sublym ideal for fragile mould.
Embossing Time: The time under heat and pressure typically ranges from 1 to 5 minutes, depending on the epoxy or SU-8 mold used, in our case was 90 seconds.
Flexdym™ chips molded via hot embossing show reliable and well-defined fluidic channels (fig2). This method is a cost-effective solution for prototyping.
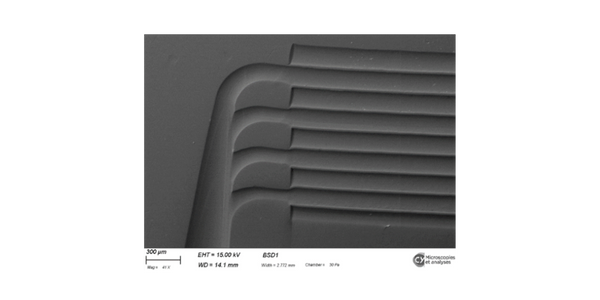
Fig2: SEM image of Flexdym™ device molded by the hot embossing machine Sublym
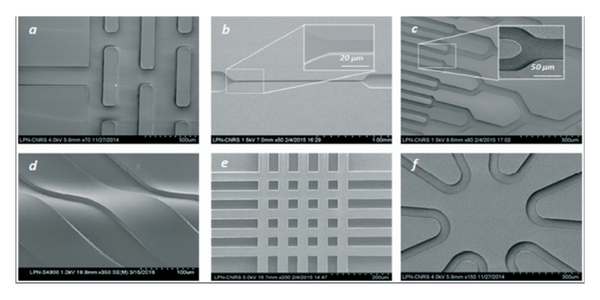
Fig3: Series of SEM, optical, and photograph images illustrating the micro structuration and assembly performance of the Flexdym™ material for various microfluidic devices. From the paper: Lachaux, Julie, et al. “Thermoplastic elastomer with advanced hydrophilization and bonding performances for rapid (30 s) and easy molding of microfluidic devices.” Lab on a Chip 17.15 (2017): 2581-2594.
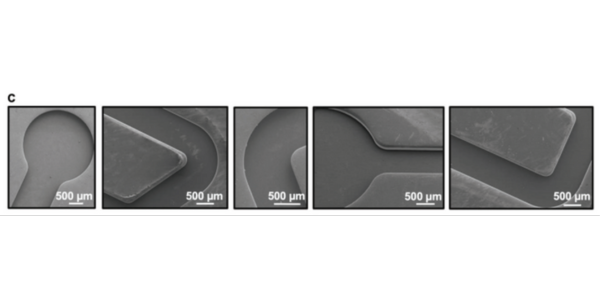
Fig4: Scanning electron microscopy images of various molded structures (e.g., channels, reservoirs) in the Flexdym™ TPS microfluidic sweat device. From the paper: Wu, Yunyun, et al. “Thermoplastic Elastomers for Wireless, Skin‐Interfaced Electronic, and Microfluidic Devices.” Advanced Materials Technologies 8.19 (2023): 2300732.
For PMMA hot embossing by using Sublym, it is possible to refer to the paper “Making Healthcare Accessible: A Rapid Clean-Room-Free Fabrication Strategy for Microfluidics-Driven Biosensors Based on Coupling Stereolithography and Hot Embossing” by H. Lu et al.
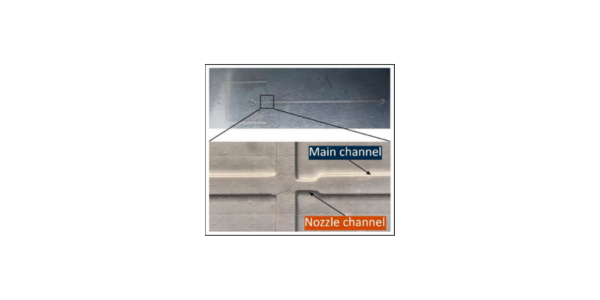
Fig5: Overview and zoom-in view of the microfluidic channel on the PMMA replica, showing well-defined channel walls and high feature integrity.
Bonding Technique
- Surface Preparation: Ensure all surfaces are clean and free from contaminants.
- Aligning the Materials: Place Flexdym™ in contact with the selected substrate, in our case thermoplastic.
- Heating and pressure application: use Sublym to apply heat and pressure/vacuum during the process at the optimal bonding temperature, specific to each polymer combination (see experimental setup).
- Time: 2 minutes ca
- Temperature: 70/80 °C
Flexdym™ chips bonded via the thermal method exhibit strong and consistent bonds with various thermoplastic substrates. Thermal bonding is particularly effective for achieving high bond strengths, with Flexdym™ chips withstanding pressures of 1.5 bar when bonded to substrates like PMMA, COC, and PS and 2 bar when bonded to Flexdym™ itself (Fig6).
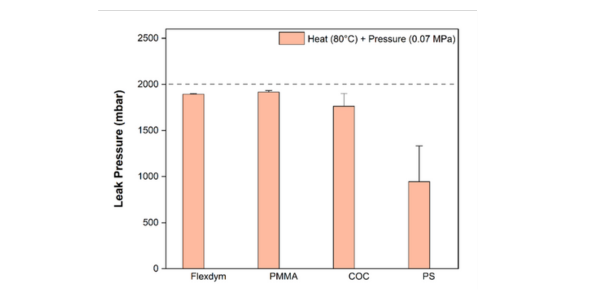
Fig6: The bond strengths of Flexdym™ chip with the selected substrate materials are shown as average leak pressures ± SEM. The dashed line represents the measurement limit. Paired Samples t-Test, **p<=0.0, n = 3-9.
The results highlight the efficiency of thermal bonding of the Flexdym™ with various thermoplastics and the possibility of using the same machine to (1) emboss the Flexdym™ with the desired pattern and (2) subsequently bond it with different thermoplastics. Optimal bonding parameters vary depending on the type of thermoplastic material but generally involve moderate to high temperatures, and a constant pressure of 0.7 MPa.
Examples of Flexdym microfluidics devices
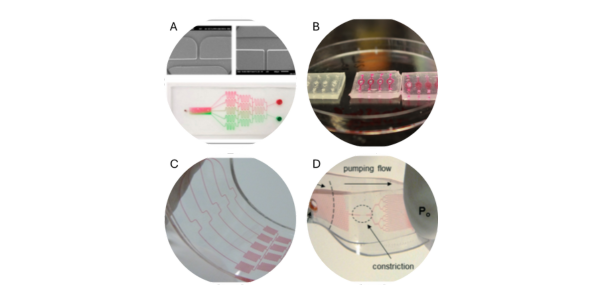
Fig6: Example of microfluidic devices fabricated in flexdym via hot embossing: A)microfluidic mixer (Nguyen, Hoang-Tuan, et al. “Low-cost, accessible fabrication methods for microfluidics research in low-resource settings.” Micromachines 9.9 (2018): 461); B) open hydrophilized microchannels device, filled with 1 mM rhodamine B and then closed for perfusion assay (); C) Gradient-like microfluidic generator network (25 × 75 mm2 device) filled with a red food colorant (); D) Photograph of a monolithic thermoplastic elastomer flexible capillary pump device maintaining a high-level and stable hydrophilic-it over the assembly.
Conclusion
The Sublym machine effectively combines hot embossing and bonding processes, making it an efficient tool for microfluidic device fabrication (saving, space, time, and money). The hot embossing of Flexdym™ is a reliable and efficient method for replicating microfluidic patterns, combining the material’s advantageous properties with the precision of the embossing process. Flexdym’s compatibility with various bonding techniques further enhances its suitability for fabricating robust and versatile microfluidic devices, offering a valuable tool for researchers and manufacturers in the field of microfluidics. Furthermore, Flexdym™ proves to be a highly versatile material for microfluidic device fabrication, offering robust bonding with multiple substrates and through various methods. Its intrinsic adhesive properties and compatibility with thermal bonding make it suitable for both low-cost prototyping and industrial-scale production.