Flexdym for Fast & Easy Microfluidic Device Fabrication
Are you having trouble advancing in your Flexdym TM experiments? Or not yet convinced Flexdym TM is the right fit for your application? Here, we break down the top reasons why you should try Flexdym TM and top tips for handling Flexdym TM for microfluidic fabrication.
Flexdym TM is a block co-polymer belonging to the SEBS (Styrene-ethylene-butylene-styrene) family of thermoplastic elastomers. If you have a biology background like myself, you are probably wondering: “What is a SEBS? And why do I care?”. Different formulations of SEBS material are commercially used in various products such as medical tubing, handle bar grips, toothbrushes, sports mouth guards, and diapers, among others (Figure 1). As the name states, these are polymers made up of styrene and ethylene-butylene chains, giving them their dual thermoplastic and elastomeric properties. Consequently, SEBS behaves like a rubber, has excellent resistance to heat and UV, and is easy to process and manufacture1. It also has high resistance to oil, weathering, heat, and can be sterilized.
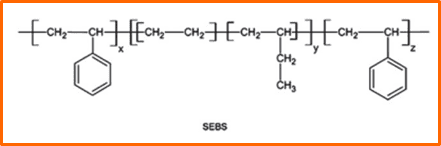
Figure 1. Chemical structure of styrene-(ethylene-butylene)-styrene (SEBS) polymers5.
However, additives including toxic phthalates, flame retardants, UV stabilizers, aging stabilizers, and latex, are often added to SEBS and other thermoplastics affecting experimental results. A range of 15 to 40 different additives can be introduced into one material, rendering it a challenging task to identify each component and its effect on the experimental reagents (i.e. surface properties, or leaching of polymeric chains). Therefore these materials may not be the best option for the fabrication of biomedical devices (e.g. sequencing, diagnostics, cell culture, or drug discovery).
Indeed, there are a few key material properties which are indispensable in most biomedical microfluidic devices: biocompatibility, optical transparency, surface properties (for functionalization and bonding), solvent resistance, and low fabrication cost.
But what sets Flexdym TM apart from other SEBS polymers? Flexdym TM is the first material to be created specifically for the microfluidics community for its features in microfluidic devices fabrication, and notably for biomedical applications. The Flexdym TM formulation was patented by our CEO, Emmanuel Roy, at the Canadian National Research Council – a material scientist who worked on point-of care diagnostics and recognized the challenges biologists face when developing chip technologies. Unlike other currently used materials which have been repurposed from other fields, Flexdym TM allows you to save on: raw material costs, device scale-up costs, microfabrication time in the lab, and the microfabrication equipment costs. Namely, Flexdym TM is biocompatible, and is oil-free and latex-free, which means no leaching of toxic ingredients into biological reagents.
FLEXDYMTM - MATERIAL PROPERTIES
As mentioned, Flexdym TM belongs to the SEBS family of thermoplastic elastomers, meaning it unites advantages of both elastomers (e.g. PDMS) and thermoplastics (e.g. polycarbonate, polystyrene, COC, etc.). This is thanks to its block co-polymer chemistry, composed of styrenic (PS) hard blocks and ethylene-butylene (EB) soft blocks2.
As other block copolymer materials, Flexdym TM is a biphasic material at macromolecular level (not blended material), which is comprised of different monomer sequences that are distributed in nanoscale domains. Nonetheless, Flexdym TM remains uniform and has a homogenous surface at scales pertinent to microfluidic systems.
This morphology provides the basis of the material performance: Rigid PS domains act as junction points, stabilizing the polymer matrix, while the dominating EB surrounding matrix offers elastomeric properties. The EB matrix has a glass transition temperature (Tg) that is negative (like PMDS), corresponding to polymeric chains that are in constant motion and giving the material its soft elastomeric nature. It provides Flexdym with conformal contact bonding capabilities, an elongation of 720%, and wearability. The second Tg is approximately 100⁰C, corresponding to the styrene blocks that work as an anchor and add rigidity for thermoforming of the material.
FLEXDYMTM - ALTERNATIVE TO PDMS
Certified Biocompatibility
Flexdym TM is a great alternative to PDMS for many reasons. Flexdym TM is certified biocompatible according to two international standards: ISO 10993 parts 4,5,6,10 & 11 and USP Class VI. This means it has been tested for cytotoxicity, skin irritation and even skin implantation (see brochure).
Low Sorption of Hydrophobic Molecules
Results also demonstrate Flexdym TM has low non-specific sorption compared to its elastomeric counterpart. Experiments where PDMS and Flexdym TM microfluidic channels were incubated for 24 hours with the dye rhodamine demonstrated a clear discrepancy in the quantity of absorbed dye after rising (Figure 2). Fluorescence intensity profiles showed a significant lack of absorption for Flexdym TM2.
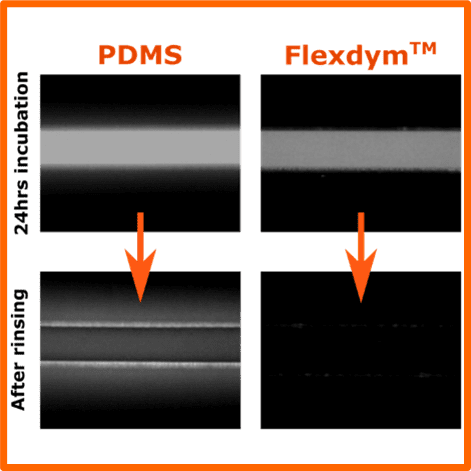
Figure 2. Flexdym TM Sorption Properties. Fluorescence microscopy images of Flexdym TM and PDMS microfluidics channels before and after 24 hours of Rhodamine B incubation2.
Flexible Polymer
Flexdym TM is a soft thermoplastic elastomer with a Young Modulus of 1.15 MPa and a high elongation of 720%, making it an ideal alternative to PDMS and for biomedical applications, such as organ-on-chip systems3,7 (see brochure), wearable sensors2,8 (see article) and blister production in point-of-care diagnostic devices8 (see brochure).
Flexdym TM’s flexibility provides easy assembly and bonding of devices via conformal contact, while maintaining the structural integrity of its features. This is a key advantage of Flexdym TM for biomedical applications, such as point-of-care devices and organ-on-chip devices, where bonding of devices fabrication from brittle materials causes channel deformation or damage, and can compromise the entire device function. Here the dimensions of micron scale features are critical to the quality of the test. For example, in the case of centrifugal devices requiring very precise flow control of different units, which must comply with security standards.
Another application of Flexdym TM is in flexible electronics and recently it has been used in flexible Organic Electrochemical Transistors (OECTs) (Figure 3). Here, the hybrid device combined Flexdym TM with PI, and the latter was inkjet-printed. For direct printing on Flexdym TM, stretchable screen-printable inks may be the most suitable option.
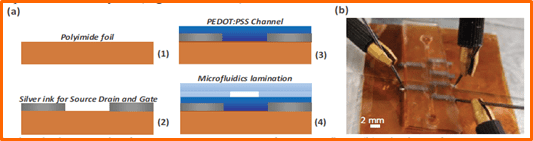
Figure 3. Flexdym TM used in flexible Organic Electrochemical Transistors (OECTs)9.
Higher Hydrophilic Stability
Another differentiating point of Flexdym TM is its hydrophilic stability. In its natural state, Flexdym TM is moderately hydrophobic, with advancing and receding contact angles of 105 ± 4° and 88 ± 4°, respectively2.
Similarly to PDMS, Flexdym TM can be treated with oxygen plasma, to render its surface hydrophilic. During this process, there is conversion of hydrocarbon units into hydrophilic groups, such as carboxylic acid. In contrast to PDMS, after plasma exposure Flexdym TM does not form a thin brittle silica layer which generates cracks. Flexdym TM’s surface retains its structural integrity and its viscoelastic properties are not compromised, thus providing conformal contact during bonding.
However, once treated with oxygen plasma, Flexdym TM reveals hydrophilic stability lasting for tested periods of up to 1 week2,3 and making it ideal for cell culture applications3,7. This is thanks to its block co-polymer nature. In elastomeric materials such as PDMS, the Tg is negative, so the polymeric chains are in constant motion and diffuse in the material. This is one reason for the rapid hydrophobic recovery often observed in PDMS. In Flexdym TM, although the EB blocks also have a negative Tg, they are anchored to the PS blocks, which prevent polymeric chain diffusion. Consequently, Flexdym TM is able to retain hydrophilic stability for longer periods of time.
No Treatment Bonding in Flexdym TM Microfluidic Device Fabrication
Flexdym TM has incredibly versatile bonding, both in terms of substrate options and protocol steps. Flexdym TM can bond to various substrates including glass and thermoplastics, such as COC (cyclic olefin copolymer), PI (polyimide), PC (polycarbonate), and PS (polystyrene). See the bonding strength in Table 1, for help selecting your substrate of choice.
The bonding mechanism is based on lamination (i.e. conformal contact), where Flexdym TM acts as a slow, soft adhesive sticking to the substrate. During this bonding process, the EB polymeric chains slowly interact and interpenetrate the substrate material intertwining across the two surfaces. Although slow, this process occurs at room temperature, which means Flexdym TM bonding does not require any harsh chemical and thermal treatments. This is ideal for many biomedical applications including diagnostics and cell culture, where the internal device surface must be functionalized (i.e. antibodies, aptamers, nucleic acid, etc.). Room temperature bonding of Flexdym TM to thermoplastics listed above requires approximately 2 to 24 hours, depending on the required bonding strength and substrate material. The fastest bonding will occur with thermoplastics PC, PS, and COC.
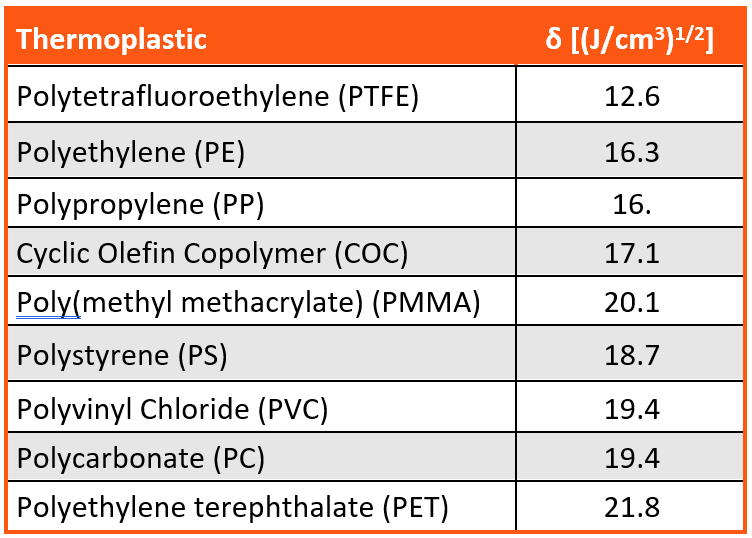
Table 1. Solubility parameters for well-known thermoplastics4.
If you are interested in fast bonding and not worried about functionalized surfaces, heat can be used to speed the process. By increasing the heat, you speed up the interaction and interpenetration process of the EB soft chains. And at dramatically higher temperatures (e.g. 100°C), the PS domains also begin to penetrate the substrate. As a guideline, we suggest heat-assisted bonding to be performed at 80°C for 1 hour.
To predict Flexdym TM’s bonding affinity to a particular substrate not listed above, the Hildebrandt solubility parameter (δ) can be used4. The solubility parameter predicts the affinity between two materials. Therefore, if we know the solubility parameter of both Flexdym TM (18 (J/cm3)1/2) and the desired substrate, the delta of these two values can be determined. The smaller the value of delta δ, the more likely that Flexdym TM will bond well to this substrate material.
Lower Permeability
Gas permeability tests have been performed on Flexdym TM 2mm thick sheets for both O2 transmission rates and CO2 transmission rates. The results reveal the gas permeability for oxygen is 7.86 Barrer & for carbon dioxide is 15.99 Barrer. However, results may differ due to a variation in the thickness of the material and the composition of PDMS (if used for comparison). For instance, when PDMS is mixed and cured the ratio of oligomers to cross-linker agents is affected by the application and user handling.
Although it presents a lower permeability than PDMS, one top application of Flexdym remains in cell culture. Various Flexdym users worldwide have published scientific articles for Flexdym hybrid devices for cell culture (Figure 4).
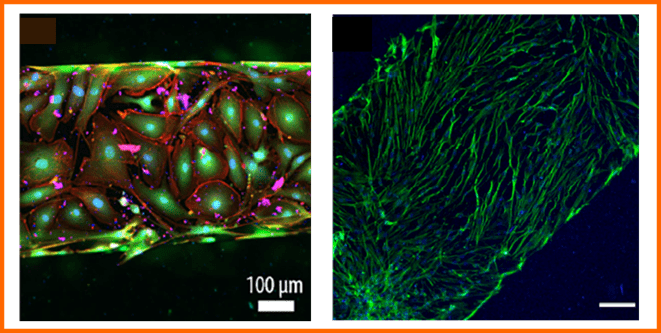
Resistance to Common Solvents
Similarly to PDMS and other thermoplastic materials used in microfluidic device fabrication, Flexdym TM is resistant to commonly used solvents such as acids and bases, as well as methanol/ethanol. It is resistant to fluorinated oils, commonly used in droplet based microfluidic applications. Also like these other materials, results show it swells in the presence of carboxylic acid and other oils. It may be important to note, it is not resistant to hydrocarbons.
FLEXDYMTM - ALTERNATIVE TO THERMOPLASTICS
Flexdym TM is a great alternative to PDMS because it possesses similar elastomeric characteristics that make it so popular with biologists. However, unlike PDMS, Flexdym is not a thermoset. Flexdym TM devices are not molded by casting, and most importantly, this is not an irreversible process. This is because Flexdym TM has thermoplastic material properties, thanks to its PS blocks. Thus, FlexdymTM is also a great alternative to thermoplastics, like COC, PC, PS and PI.
Recyclable Material
Flexdym TM is molded through hot embossing, which uses the parameters of heat, pressure, and time to convert it into a molten state and fill the cavities of the mold. This is accomplished in an isothermal process, which provides Flexdym TM with its unique fast molding protocol. This process can be done by using a hot press or a hot embossing, such as our low-cost and compact Sublym machine. When using the Sublym, Flexdym TM can be molded in as little as 30 seconds, depending on the mold size, material, and feature design.
Another great advantage of this replication process is that once FlexdymTM is used, it can be re-molded (watch our youtube video: How To: Recycle & Re use Flexdym). Even if it has been assembled in a chip and used for an experiment, it is possible to sterilize it and re-mold it again. Reported methods of sterilization include ethylene oxide, gamma irradiation, or autoclave.
Surface Functionalization
The surface of Flexdym TM can be functionalized similarly to other thermoplastics, including through EDC-NHS amine-based reactions, and silane-based reactions (see blog post). This can be accomplished by first activating the surface with plasma activation.
Amine-based reactions are a classic method for functionalizing proteins on substrates. On its outer surface, the protein will present the primary amines (-NH2) which can bond with various chemical groups, such as NHS esters, through acylation or akylation reactions6. The carboxyl groups on the surface of Flexdym TM are activated with a carbodiimide derivative. EDC then reacts with the activated Flexdym TM surface to form active O-acylisourea intermediate, which is stabilized using S-NHS (N-hydroxysulfosuccinimide). Finally, EDC couples SNHS to the carboxyl groups producing an S-NHS-activated site. Both O-acylisourea intermediate and S-NHS-ester formed are amine-reactive, but at pH 7-9 the S-NSH-ester has much greater stability. Finally, these intermediates react with primary amines of proteins to form amide bonds (Figure 5).
In silane-based functionalization, the silane coupling agent possesses a hydrolyzable group (i.e. alkoxy, acyloxy, halogen or amine), which when hydrolyzed produces a reactive silanol group. It can then assemble with other silanol groups to form siloxane linkages. In the reactive silanol, the R group is a nonhydrolyzable organic radical that may be functionalized. Finally, the reaction of an organosilane with a substrate can be multipurpose, including for altering substrate wetting, substrate adhesion, or functionalizing the substrate to catalyze biochemical reactions. Most importantly, it provides a method of covalent bonding between organic and inorganic materials10.
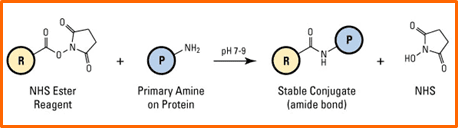
Figure 5. Reaction scheme for NHS-ester amine-based functionalization reactions6.
Fast & Easy Prototyping
Fabrication of full or hybrid Flexdym TM devices is a fast, easy and low-cost procedure which renders microfabrication extremely user-friendly. Moreover, it is a material that allows for a seamless scale-up progression, from prototyping and R&D to clinical testing and mass production.
Flexdym TM molding occurs rapidly thanks to its low viscosity (similar to other SEBS) approximately 3 to 6 orders of magnitude lower than hard thermoplastics (see Flexdym TM brochure). Using the Sublym hot embossing machine, Flexdym microfluidic device fabrication can take as little as 10 minutes for both molding and device assembly (see How To: Molding Flexdym with SU8 Mold video), depending on parameters such as device size, feature resolution, feature aspect ratio, and mold material (Figure 6). Flexdym TM sheets and pellets can both be used with the hot embossing procedure, although we recommend using sheets over the pellets, for a cleaner and more transparent finish.
Once the device has been assembled, bonding can take from 2 to 24 hours depending on the temperature of the process. Again, the great advantage of Flexdym TM bonding is that it does not require surface treatment or adhesives. This greatly simplifies the process and reduces costs.
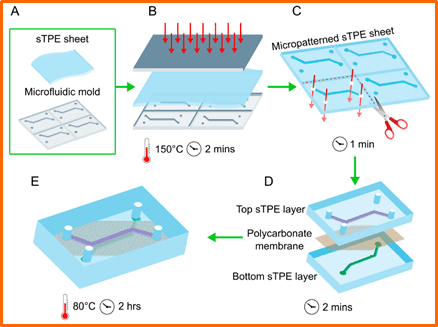
Figure 6. Microfluidic device fabrication protocol length for a two chamber membrane-integrated cell culture device using Flexdym TM and a polycarbonate porous membrane3.
For small scales of production, Flexdym TM is available in starter pack and roll formats. The starter pack format includes 10 sheets (15 x 15 cm), and is the least cost-effective option. However it has been designed purely for initial testing of the material, to determine its fit for the application. But what are the costs?
For demonstration purposes, if we consider a microfluidic hybrid device composed of one sheet of Flexdym TM combined with another substrate, measuring the size of a microscopy slide (75 x 25 mm), then we can calculate the costs. From one starter pack, there can be 120 devices made, which results in $3 per device. Of course, as you boost your production with Flexdym TM rolls or pellets, the costs reduce considerably to as little as a few cents per device thanks to economies of scale.
There are also additional cost savings in terms of equipment and time. For example, Flexdym TM devices do not need to be fabricated in a clean room environment and the equipment is low-cost, i.e. no regular fees for clean rooms and no oxygen plasma required for bonding. In addition, the Sublym hot embossing machine is 50-fold less expensive than other commercially available hot embossing machines, and dramatically more user-friendly than classic hot press machines.
Overall, with little initial investment, the Flexdym TM fabrication technology for microfluidic devices allows for faster fabrication, faster results, and faster progress.
Low Cost Scale-Up
Microfluidic device fabrication using thermoplastics can be accomplished using a variety of methods including hot embossing, injection molding, or hot roll-to-roll embossing into polymer foils using high throughput reel-to-reel processing4. The same applies to Flexdym TM and its different formats: Flexdym TM sheets can be used for mass production via roll-to-roll embossing, while Flexdym TM pellets are compatible with the mass production method of injection molding.
Consequently, Flexdym TM provides researchers the opportunity to develop their research from start to finish, using the same material. This has been a key challenge in the field of microfluidics, as academics often prefer PDMS as their material of choice, whereas industrials lean towards thermoplastics because of scalability. Flexdym TM aims to fill this gap and help propel the commercialization of more microfluidic technologies.
In the case of injection molding using Flexdym TM pellets, we have performed tests using the Arburg Allrounder 320C Golden Edition (barrel diameter 25 mm) with plaque size (150x110x2 mm) (Table 2). These parameters serve as a point of reference and may vary depending on the brand and model of the injection machine used.
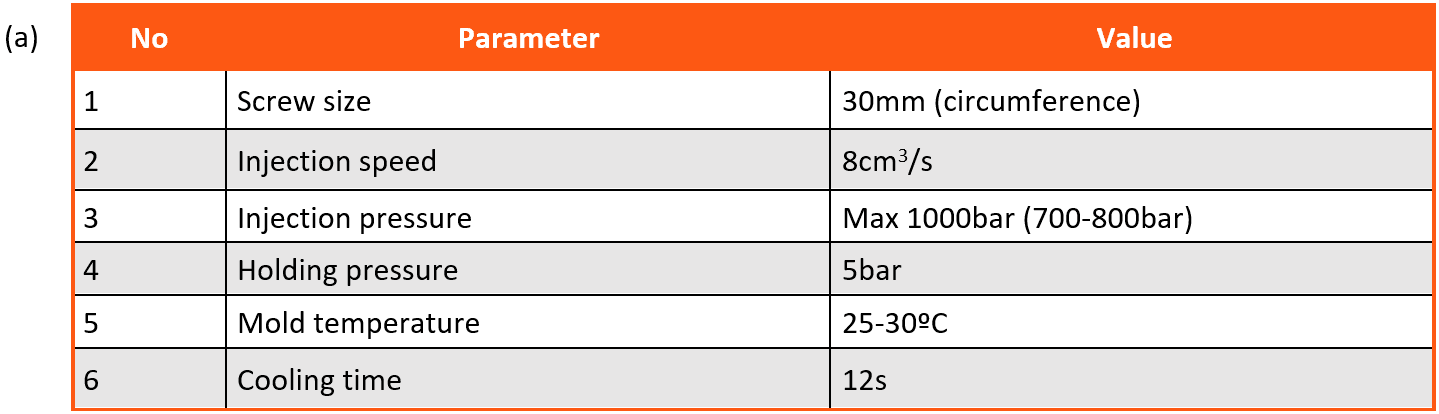

Table 2. Flexdym TM injection molding parameters for Arburg Allrounder 320C Golden Edition (barrel diameter 25 mm) with plaque size (150x110x2 mm).
Additionally, successful preliminary tests have been conducted for 3D printing of FlexdymTM pellets by the team at the 3D.FAB platform in Lyon, France (see video soon). The resolution and material transparency are in the process of being investigated, but these results show a promising future for FlexdymTM in 3D printing of microfluidic devices.
FLEXDYMTM - TROUBLE SHOOTING
As the Flexdym TM user community is growing quickly across the world, in both academia and industry, we have rounded up the top most recurring trouble shooting issues researchers encounter while using Flexdym TM. Hopefully these tips will help you move forward more quickly in your microfluidic device development!
Flexdym Molding Parameters
If you are a first timer user of the Flexdym TM sheets and the Sublym hot embossing machine for device fabrication and are unsure of what parameters to start with, watch our youtube video How To: Molding Flexdym with SU-8 silicon wafer.
The process will depend on various parameters including the size of your mold, the features and the mold materials. However we provide in Table 3 reference starting points below.

Table 3. Flexdym TM molding parameters for the Sublym hot embossing machine.
Testing Before Investing
If you are a first timer user of the Flexdym TM and are not in possession of a Sublym hot embossing machine, there are two alternative options to test the principles of Flexdym TM molding. The first option is to use a classic hot press, commonly found on most university campuses, and the second option is to mimic the process using an oven and a weight. We are currently in the process of optimizing the latter option and will soon share the results.
Flexdym Handling
Flexdym TM sheets are protected from contaminants by an transparent film on both sides. When handling the material, we recommend keeping the protective films on until the moment it is sandwiched between the counter mold and the mold.
When cutting the Flexdym TM using scissors, we recommend leaving the protective film on, in order to facilitate the cutting process (see our video How To: Handle Flexdym Sheets TM). Other methods of cutting Flexdym TM include hot knives (heat provides a clean finish), die cuts (for standardized shapes), lasers, and water-jetting. Both femto-second lasers and CO2 lasers can be used to cut and pattern Flexdym TM, with varying results depending on the machine model & brand.
Note – when cutting Flexdym TM it may be useful to remove the protective film and allow the material to relax under a fume hood in order to reduce any shrinkage effects.
Once you have molded Flexdym TM and removed the counter mold-Flexdym TM-mold sandwich from the Sublym or hot press, the unmolding step becomes critical. For easy un-molding, please wait until the counter mold is warm to the touch and slowly remove the Flexdym TM-mold from the counter mold with the help of isopropanol and flat tweezers. For additional help, you can watch our youtube video How To: Unmolding Flexdym TM.
Bonding Strength
The bonding technique of Flexdym TM to a substrate can vary depending on the material’s chemistry. For example, Flexdym TM has the lowest bonding strength when combined with glass. Here, we do not recommend surpassing 700 mbar in fluidic pressure, which is not an issue for most cell culture applications.
In the case where higher bonding strength is required, we recommend using Flexdym TM itself or other thermoplastic substrates for the microfluidic device. Flexdym TM bonds well to most commonly used thermoplastics including COC, PI, PS, and PC. It this case the fluidics pressures of up to 2 bars have been tested successfully.
However, please bear in mind that there are variations in the bonding quality in function of the material grade or brand. For example, Kapton® is a brand of polyimide which is known to bond particularly well to Flexdym TM. See the Table 4 below for a list of polymers providing good bonding strength.
Another important tip: Please ensure good conformal contact during lamination of Flexdym TM onto the substrates. As the Flexdym TM sheet is laid on its substrate press on the material to get rid of air bubbles and ensure homogenous contact throughout the entire surface of the device. Note – pressure is not required to be maintained during the process. Watch our youtube video for reference: How To: Flexdym Bonding to Different Substrates.
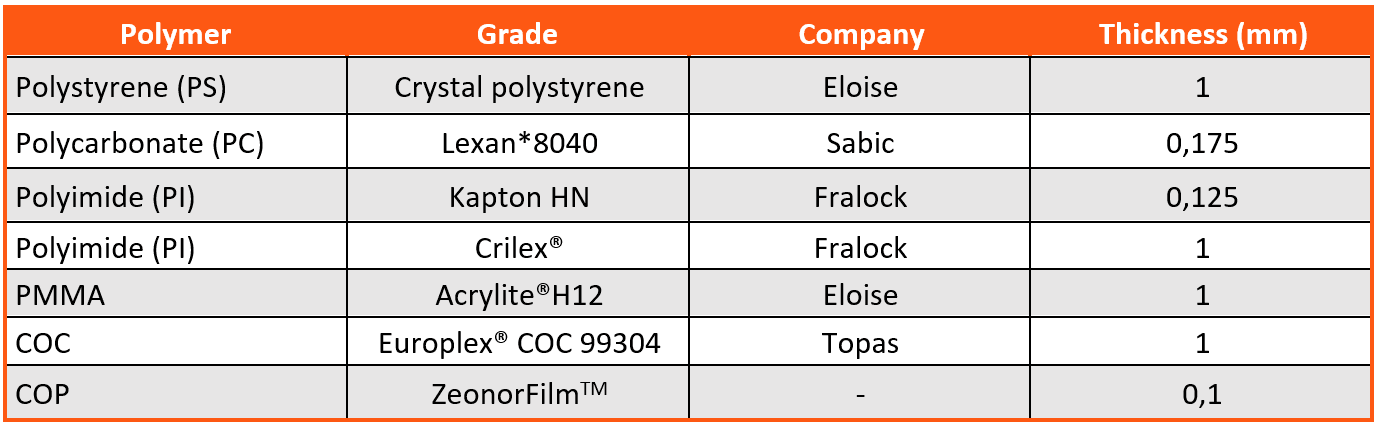
Table 4. Commercially available thermoplastics tested for good bonding strength with Flexdym TM. For each of these, burst pressures up to 2 bars were tested.
Bubble Formation
When molding Flexdym TM, it is possible that air bubble formation appears in the material. In this case there are a few points to review. First consider your 2 key molding parameters: time and temperature. Depending on your mold size and material, the temperature may not be high enough for material flow to be accomplished.
CONCLUSION
Harnessing our Flexdym TM technology, at Eden Tech we aim to reinvent microfluidics and make it more accessible throughout the scientific community and beyond. Since we first commercialized our material around 2 years ago, our Flexdym TM user base continues to grow tremendously, stretching across the globe in both academia and industry. There are over 150 Flex users worldwide and we have two distributors.
If you are still wondering whether Flexdym TM is a good fit for you, then consider the following:
- Are you seeking a competitive advantage in the development of your next device?
- Are you under time pressure to achieve fast results for an article submission deadline or product development?
- Are you frustrated with complicated protocols, the need for clean room infrastructure and expensive machinery?
- Are you facing product development threats because of non-scalable materials?
If so, our original microfabrication solutions may help you overcome your obstacles. We cover the key material needs of microfluidic device fabrication, especially in biotech applications. But we also offer a material that is scalable & affordable, and with a fast & easy microfabrication protocol.
References
1. Polymer Properties database: https://polymerdatabase.com/Polymer%20Brands/SEBS.html
2. J. Lachaux et al. (2017) Thermoplastic elastomer with advanced hydrophilization and bonding performances for rapid (30 s) and easy molding of microfluidic devices, Lab on a Chip, 17, 2581.
3. A.H. McMillan et al. (2020) Rapid Fabrication of Membrane-Integrated Thermoplastic Elastomer Microfluidic Devices, Micromachines MDPI, 11, 731.
4. C.W. Tsao and D.L. DeVoe (2009) Bonding of thermoplastic polymer microfluidics, Microfluid Nanofluid, 6: 1-16.
5. K. Polat et al. (2014) Nano and microstructures of SEBS/PP/wax blend membranes: SAXS and WAXS analyses, J Polymer Engineering.
6. Thermofisher Scientific: Protein Biology Resource Library, Amine-Reactive Crosslinker Chemistry
7. H. Salmon et al. (2021) Facile engineering and interfacing of styrenic block copolymers devices for low-cost, multipurpose microfluidic applications, Engineering Reports.
8. E. Roy et al. (2015) From cellular lysis to microarray detection, an integrated thermoplastic elastomer (TPE) point of care Lab on a Disc, Lab on a Chip, 15, 406.
9. S. Demuru et al. (2019) A Flexible platform with inkjet-printed organic electrochemical transistors integrated in microfluidics for selective ion detection, Conference Paper.
10. Silane Coupling Agents: Connecting Across Boundaries (3rd Edition) by Barry Arkles with selected updates by Annalese Maddox, Mani Singh, Joel Zazyczny, and Janis Matisons ©Copyright 2014 Gelest, Inc. • Morrisville, PA.
Dr. Roberta Menezes
Interdisciplinary Ph.D. from University of Paris & ESPCI Paris.