FLEXDYM™
STARTER PACK | ROLLS | PELLETS
The Flexdym™ Solution
Flexdym is the first material tailored explicitly for microfluidic chips. It is flexible, easily molded, bonded, transparent, and resistant to the adsorption of small particles.
Use the flexdym material at all scales, from prototyping to mass production of your chips.
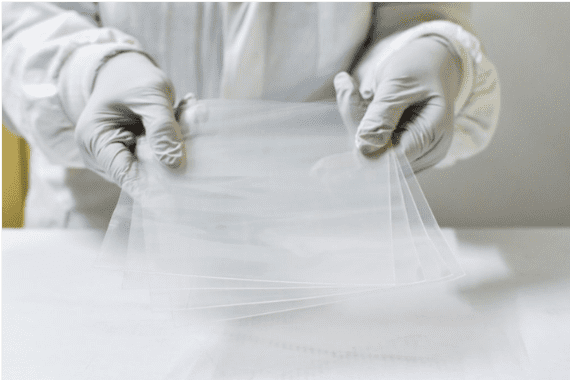
Flexdym Starter Pack
Primarily, the starter pack is the perfect format for first-time Flexdym users to test the material for their application. Moreover, within one starter pack, different thicknesses can be mixed, making the selection process easier for you.
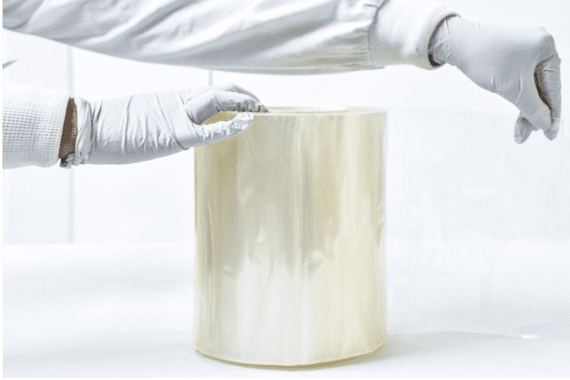
Flexdym Rolls
Following initial testing, the Flexdym Rolls offer a more cost-effective format for users. Furthermore, they are compatible with roll-to-roll embossing methods for mass production.
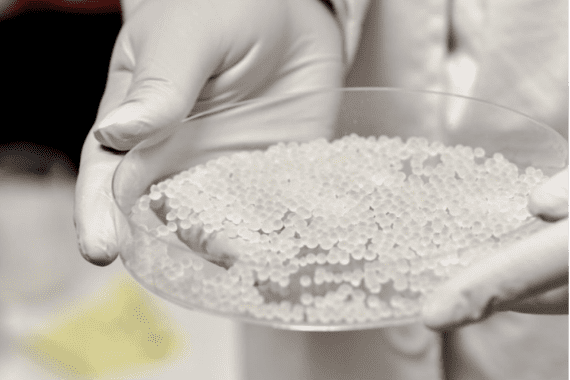
Flexdym Pellets
For experienced users, the Flexdym Pellets are ideal for those who have developed a marketable product using this technology. Subsequently, they are suitable for beginning mass production or 3D printing with our Flexdym pellets.
From Micro to Nano-Sized Structures
Flexdym microfluidic chips are molded and replicated via hot embossing, which allows the replication of structures at higher levels of accuracy and precision than soft lithography.
DEVICE REPLICATION
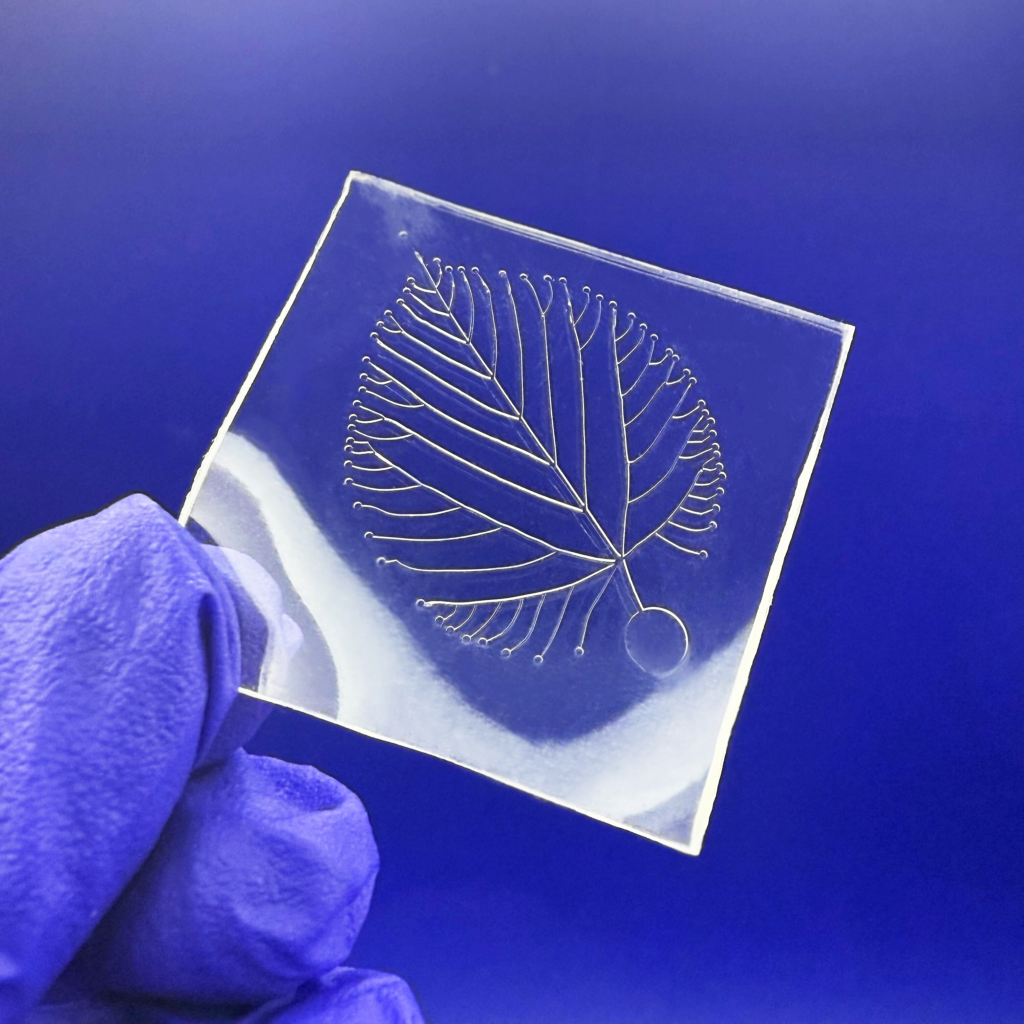
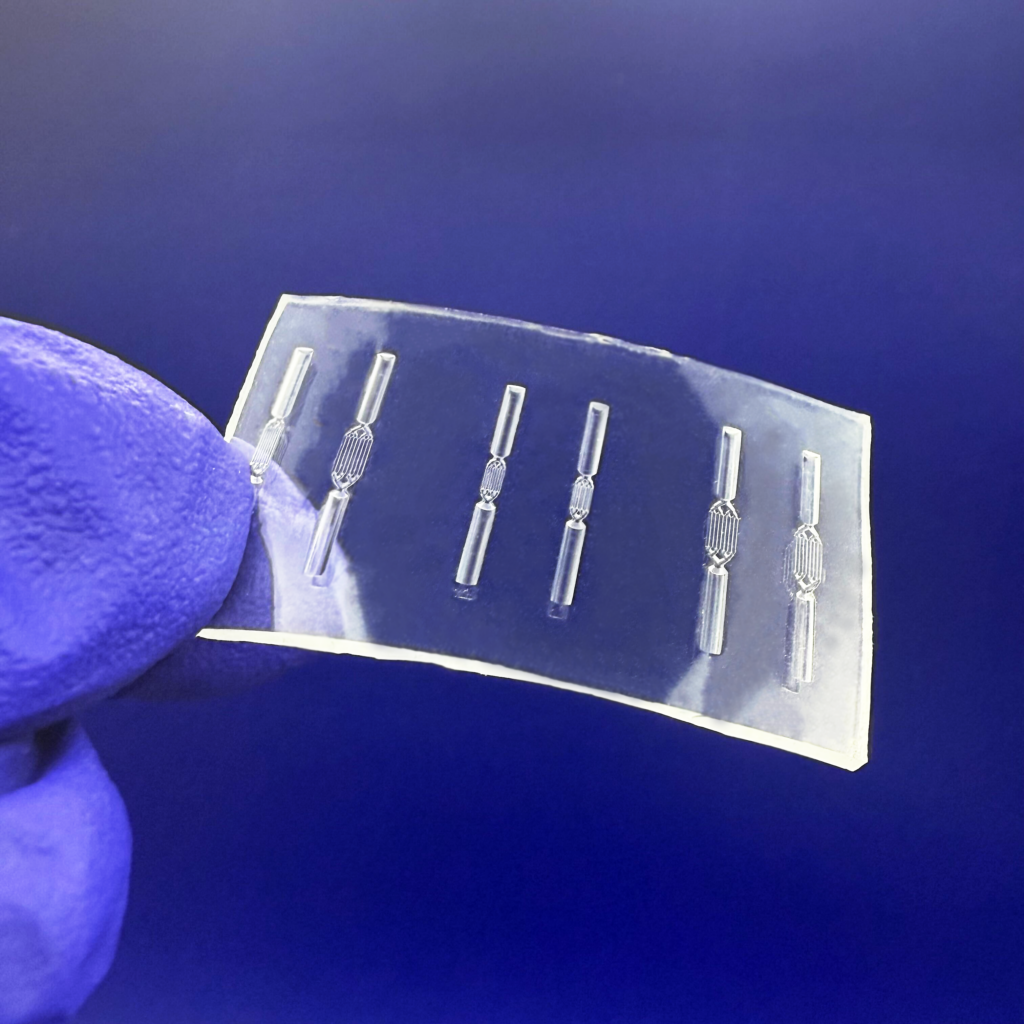
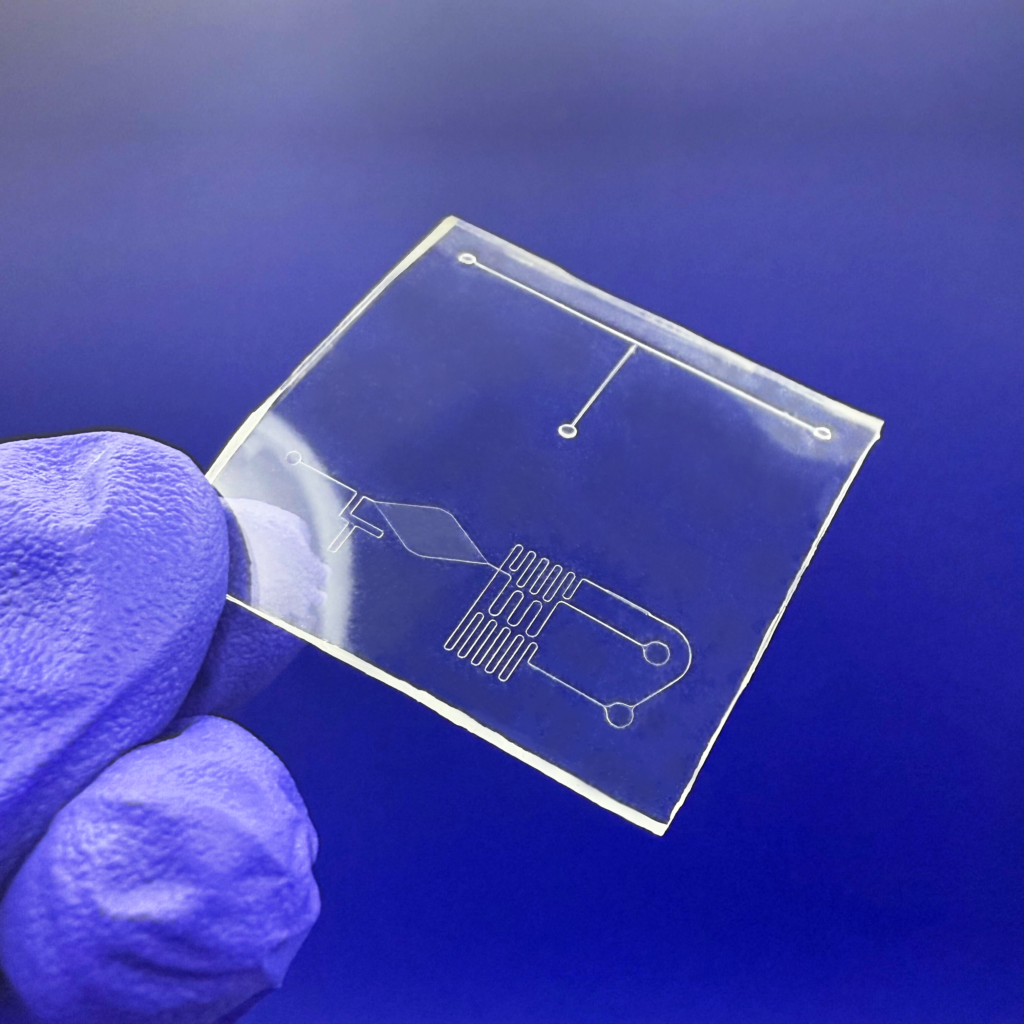
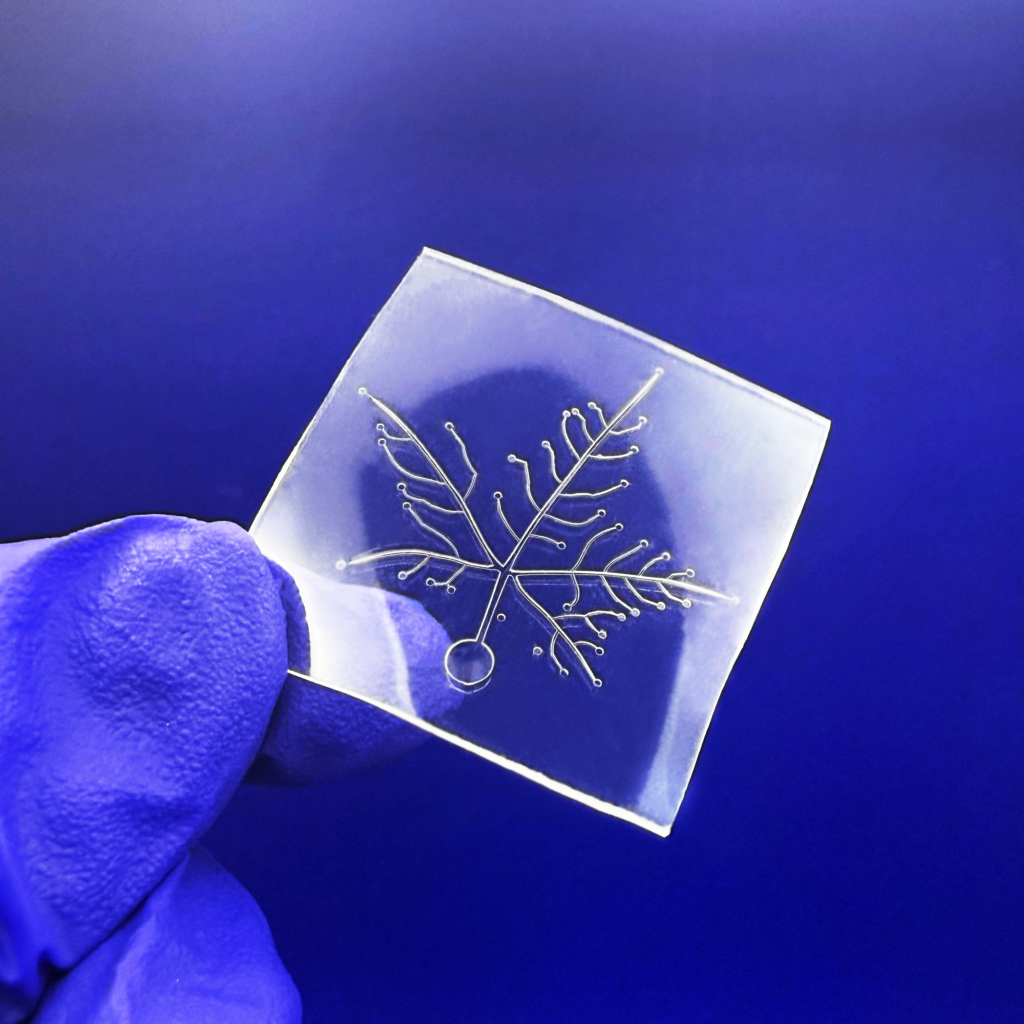
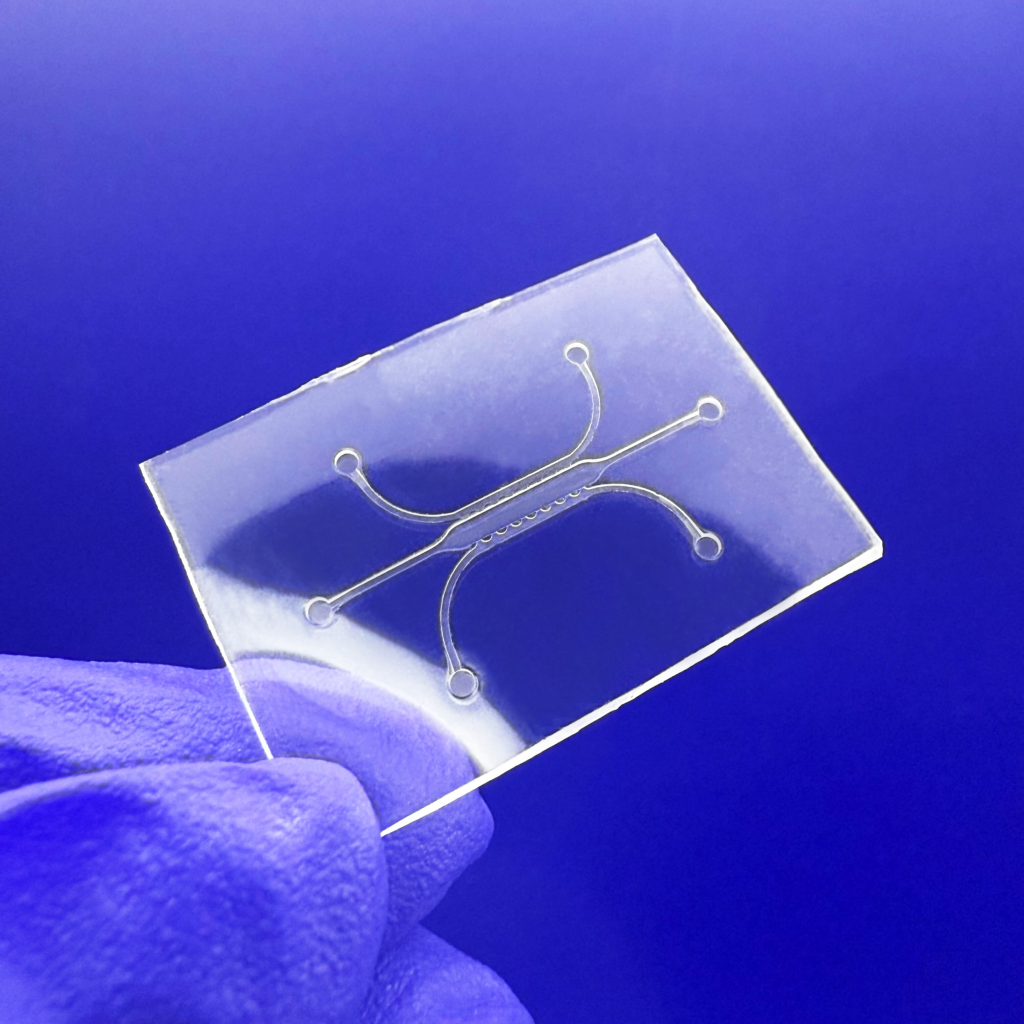
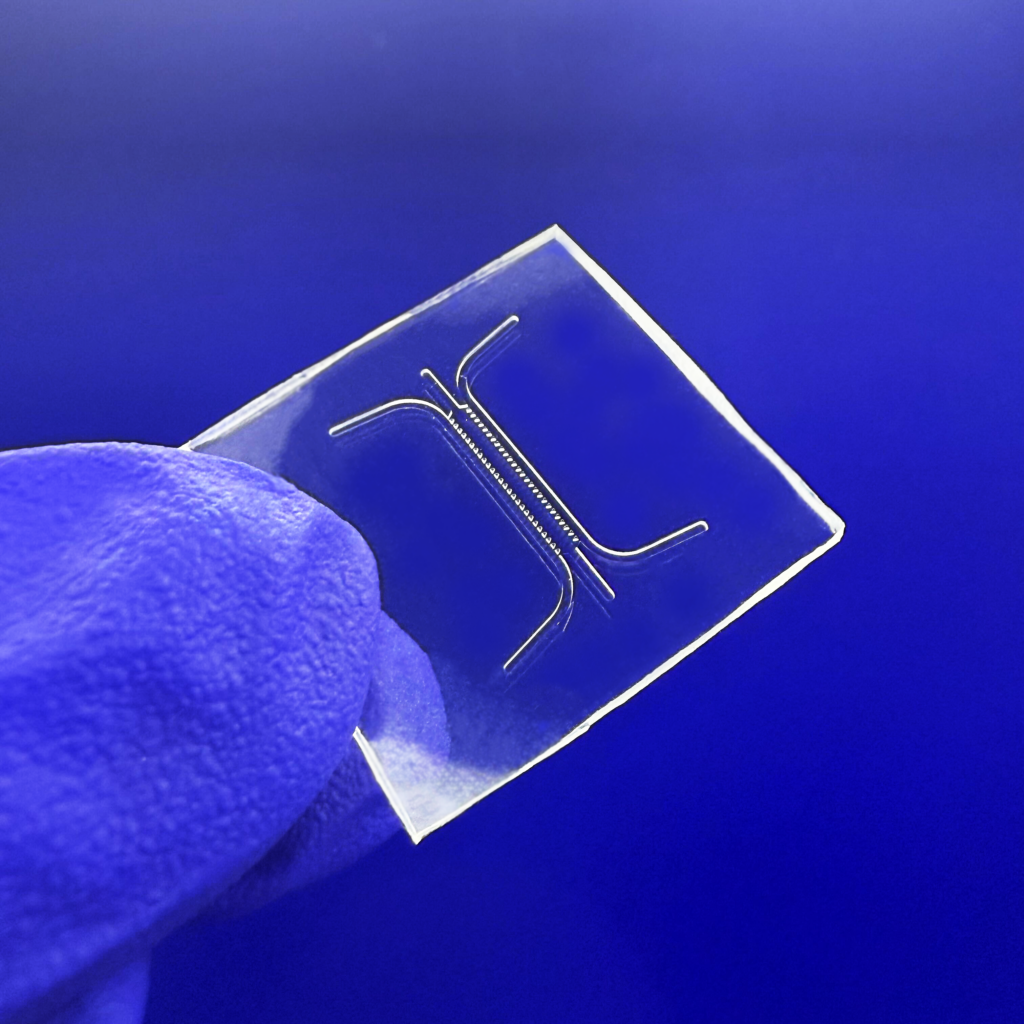
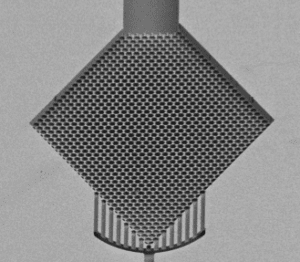
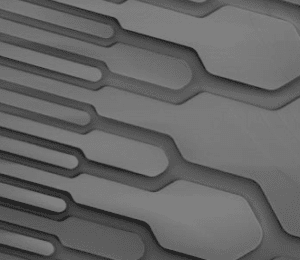
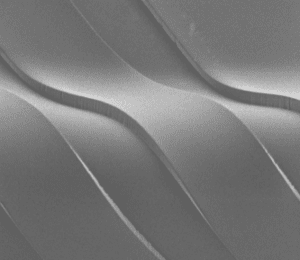
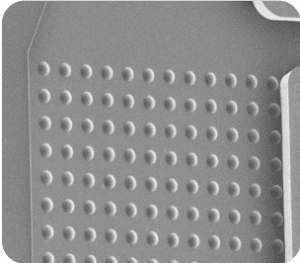
Easy Steps for Flexdym Microfluidic Chips
01
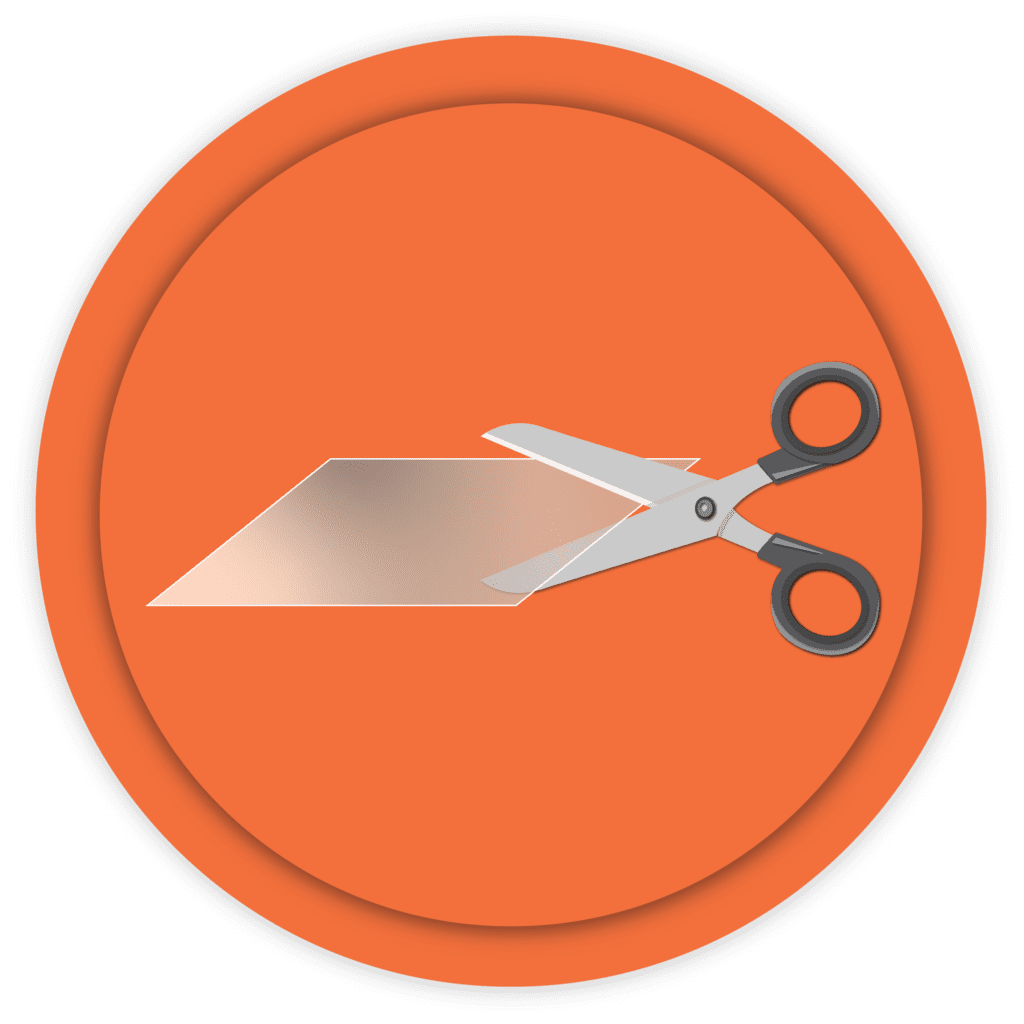
Cut It
First, cut a protected Flexdym sheet using your preferred method, immediately rendering the material usable without further preparation.
02
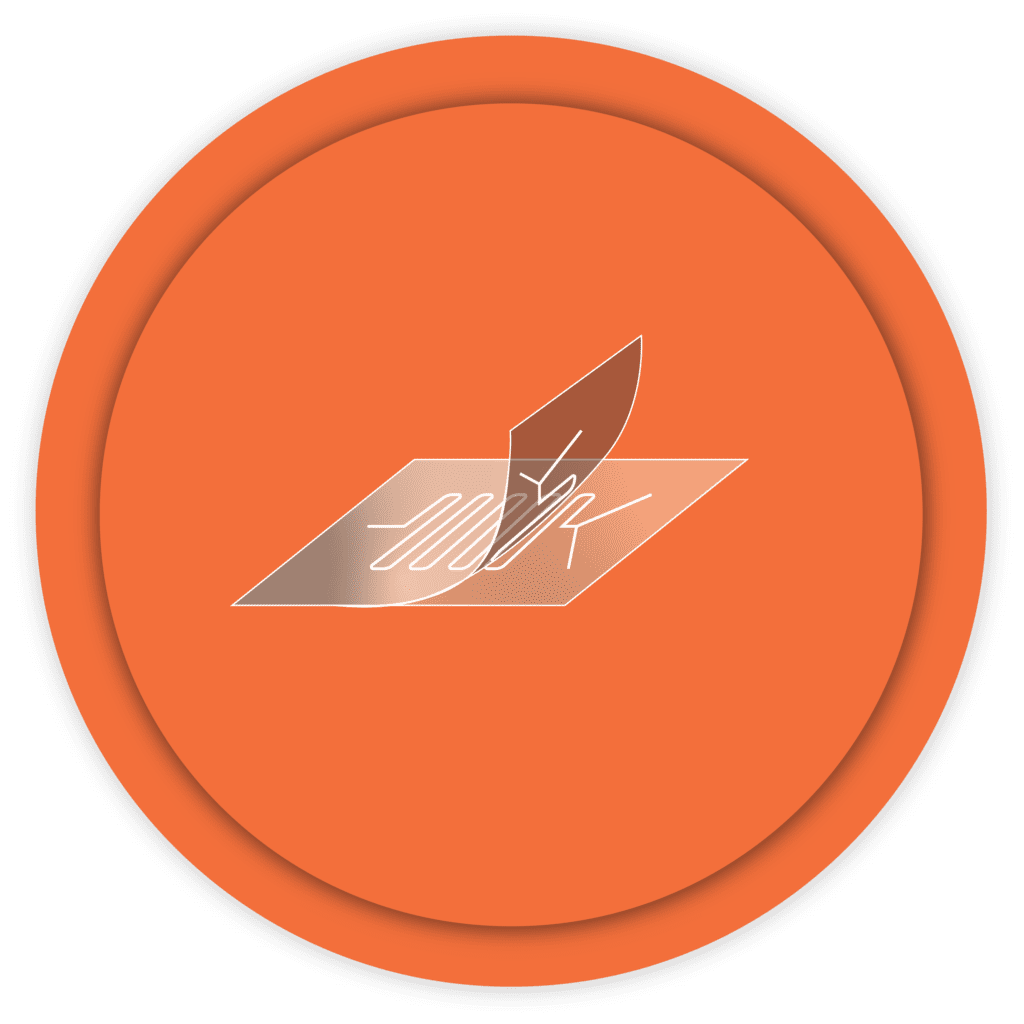
Press It
Next, remove protective films and apply heat and pressure to the Flexdym sheet between molds.
03
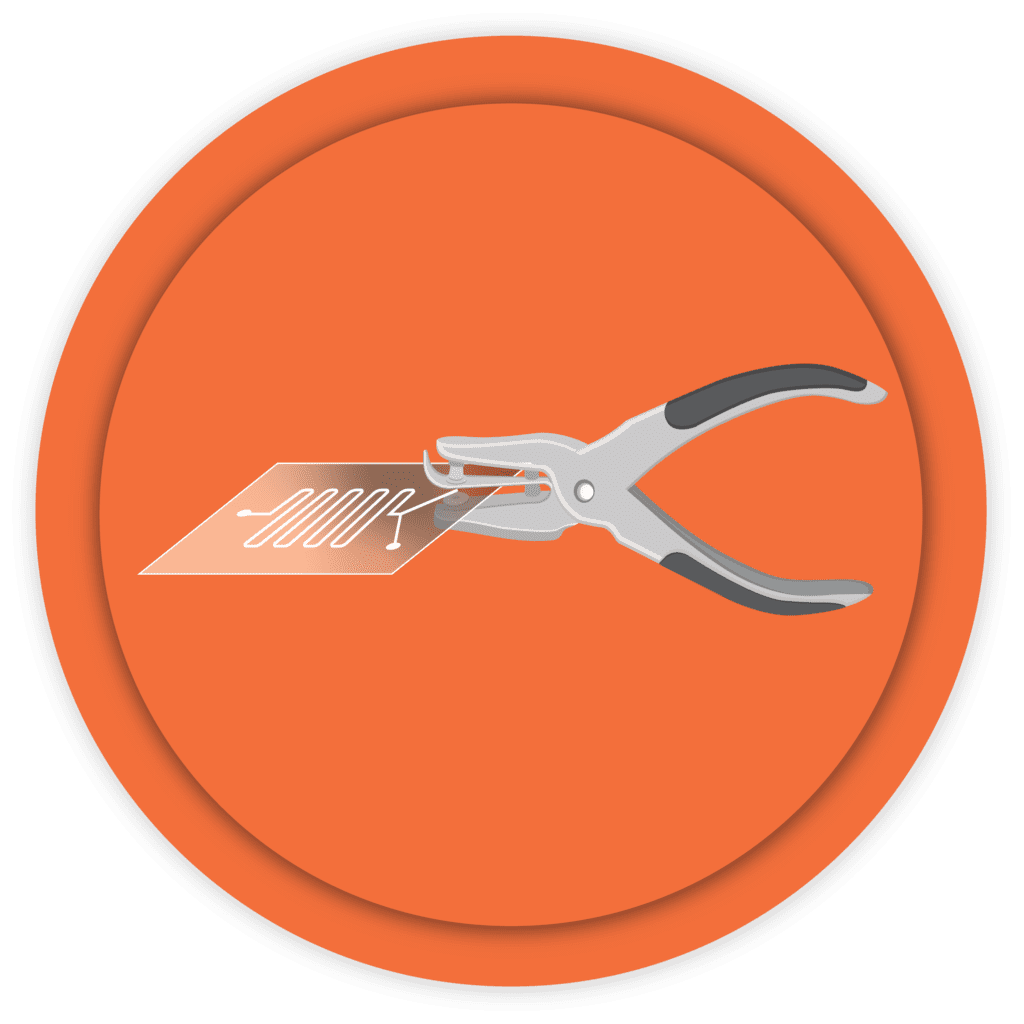
Create Inlets
Following molding, protect the Flexdym sheet and create inlet/outlet ports.
04
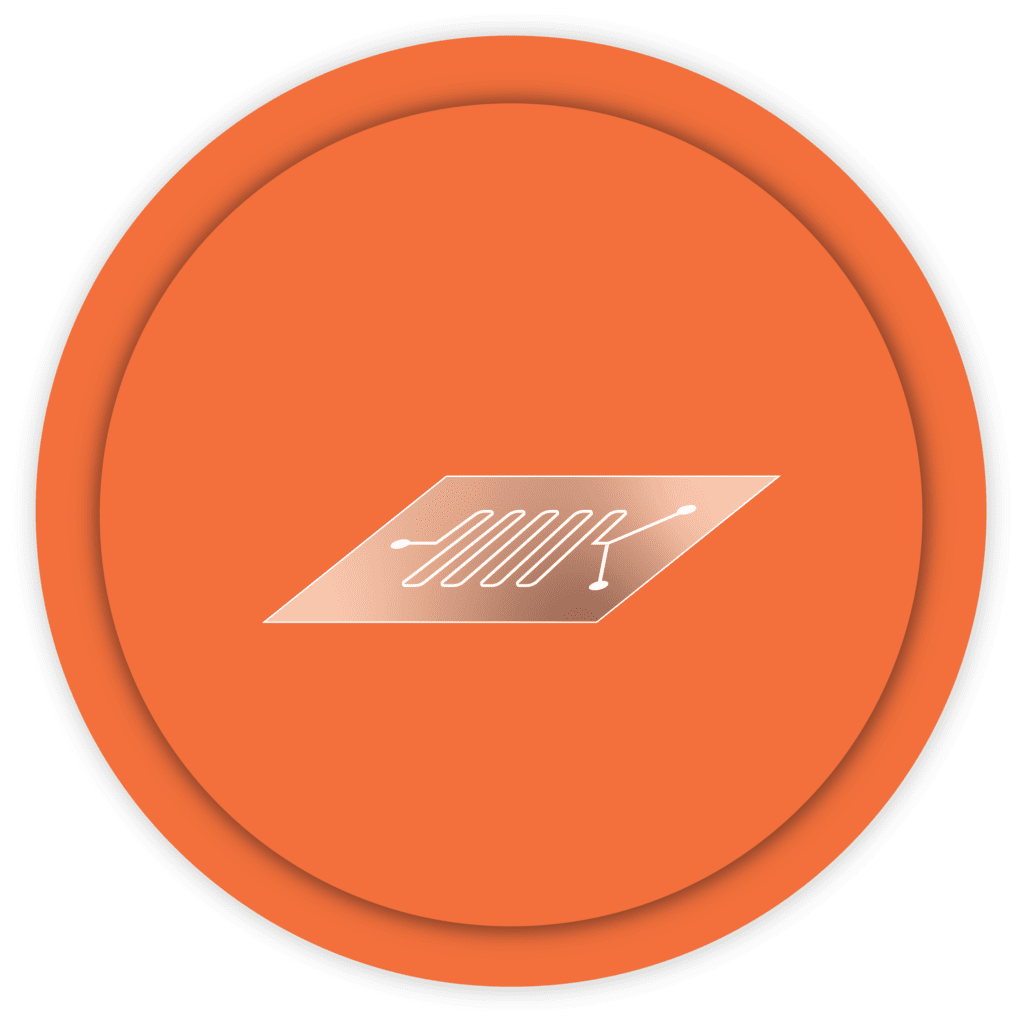
Place It
Finally, remove the protective sheet and assemble the Flexdym with your chosen substrate, leveraging its conformability for optimal contact.
Looking to Test Out Flexdym?
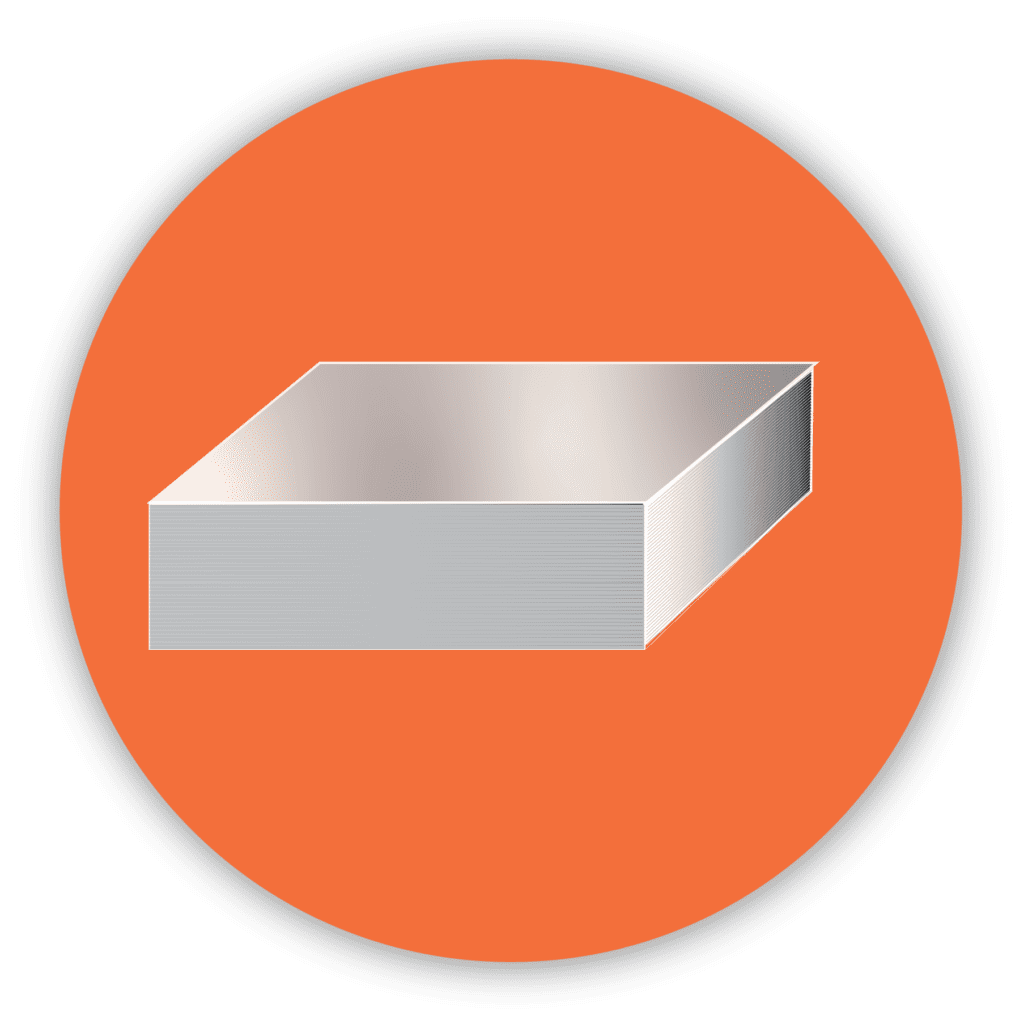
The starter pack contains 10 sheets of 15 x 15 cm Flexdym, wrapped in 2 protective transparent films.
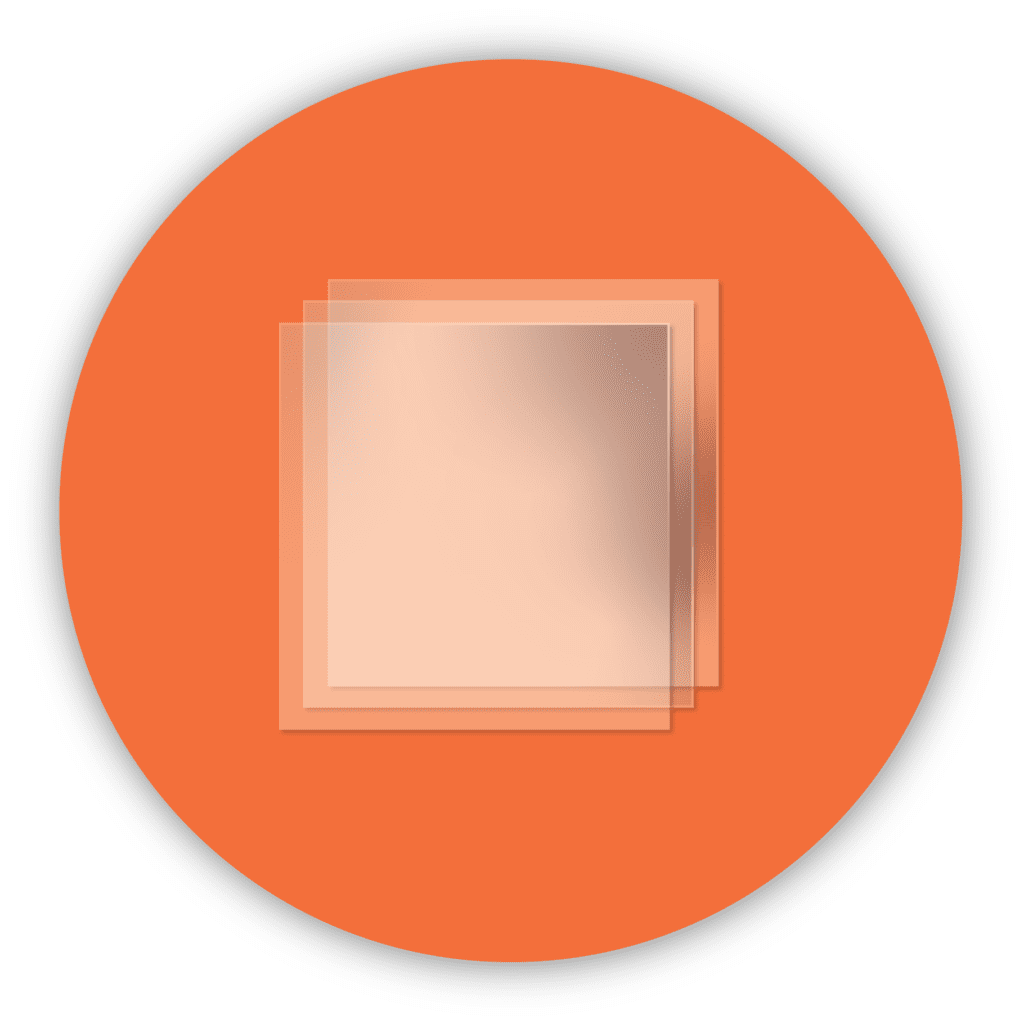
In one pack choose between a range of thicknesses: 0.25, 0.75, 1.2, or 2 mm. Mix these according to your preference.
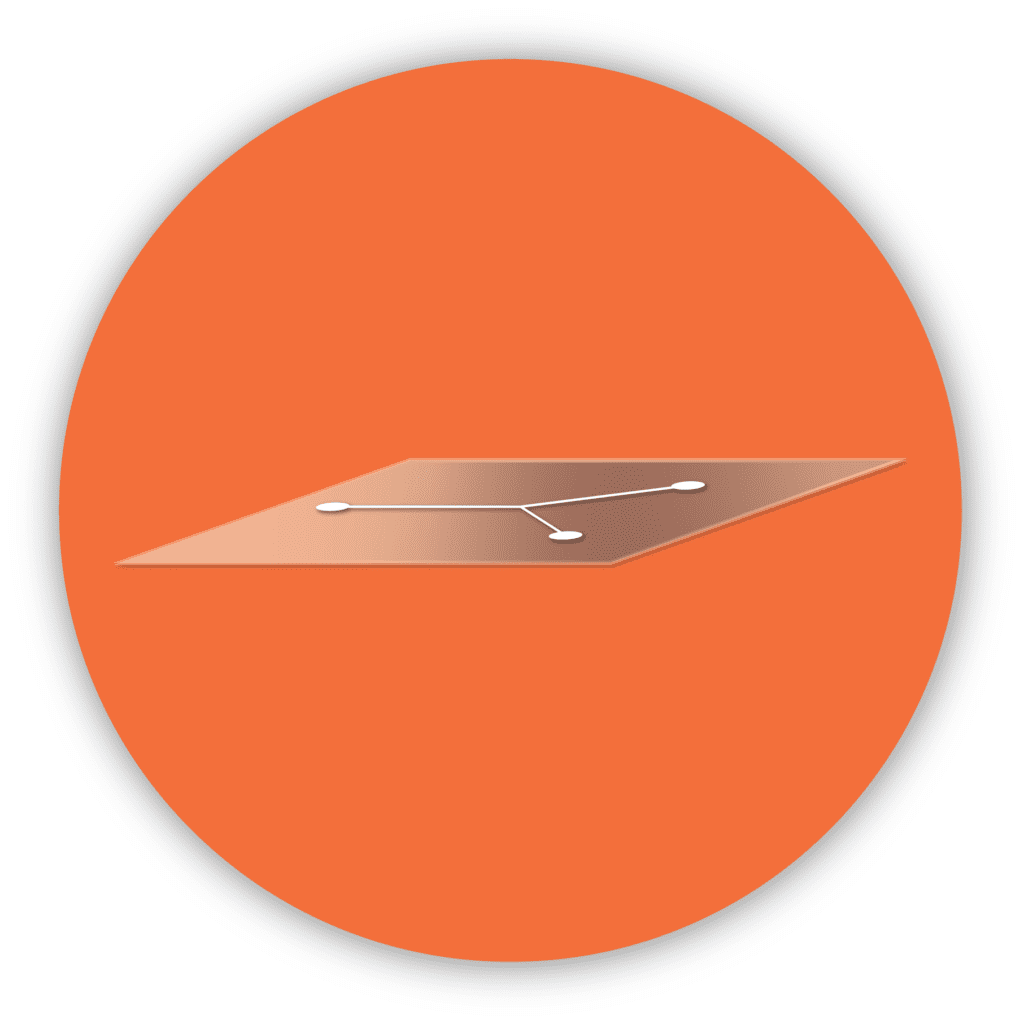
Each sheet can be cut using scissors & molded using a hot press. Depending on the size of the mold, the process can last from 30 s to 15 min.
Flexdym Handling
Initially, a Flexdym sheet is protected by films on both sides to prevent contamination. Therefore, retain the films during cutting. Subsequently, remove them when preparing to sandwich the sheet between molds.
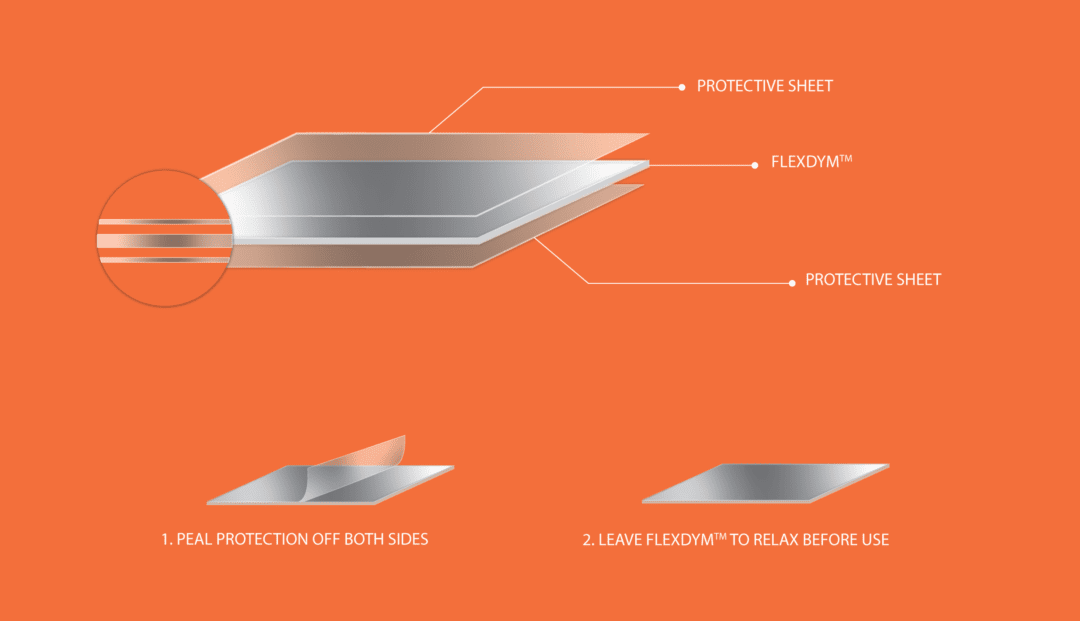
A Biocompatible Material that is Scalable
From Prototyping...
Use Flexdym starter packs or rolls to create chips quickly and easily. Mold Flexdym in as little as 30 seconds using our Sublym machine. The full Flexdym protocol length is approx. 15-20 minutes, depending on mold design, mold material, feature resolution, design size, etc.
...to Mass Production.
The Flexdym pellets are compatible with 3D printing and injection molding processes used in mass production. Flexdym sheets can also be used to mass produce devices via roll-to-roll embossing. Now you have the opportunity to turn you technology into a commercial product.
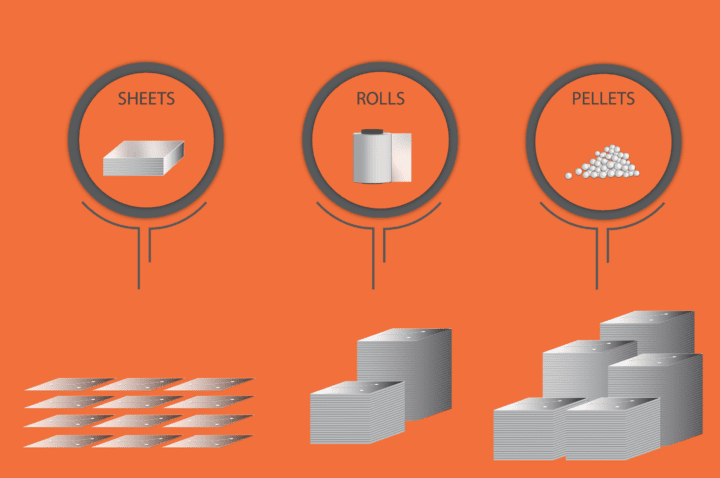
Flexdym Pellets for Mass Production
Primarily, Eden Tech developed Flexdym pellets for cost-effective mass production. Specifically, they are designed for injection molding or 3D printing. Alternatively, they can facilitate small-scale production using a standard hot press.
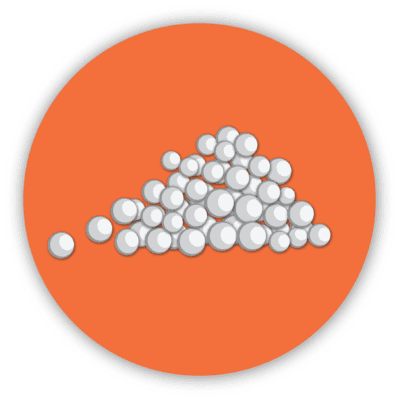
Flexdym Pellets are available per kilo.
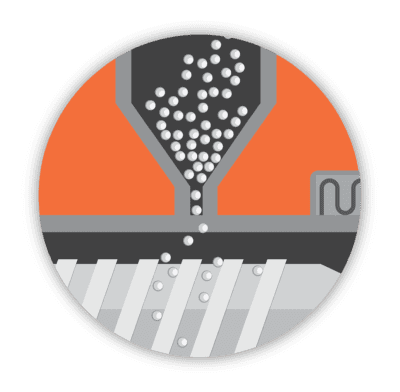
The pellets can be molded at small scales, suing our Sublym or a hot press, and at large scales using injection molding or 3D printing.
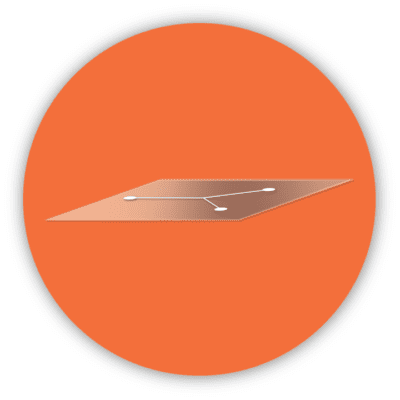
The injection molding process allows Flexdym devices to be mass produced - a key advantage for product development.
Injection Molding for Mass Production
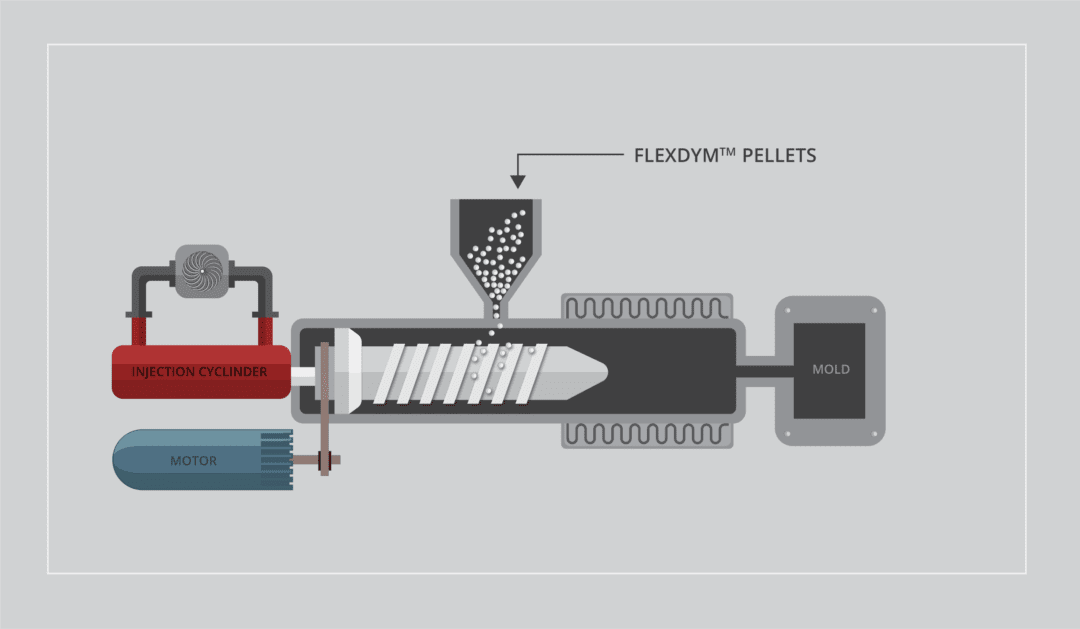
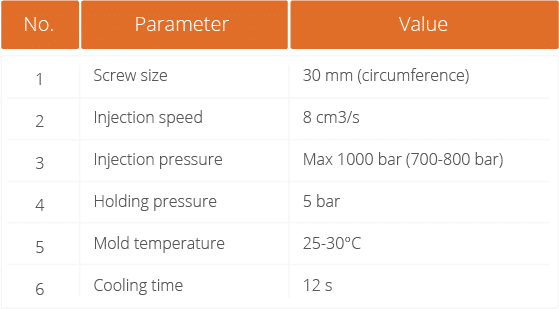
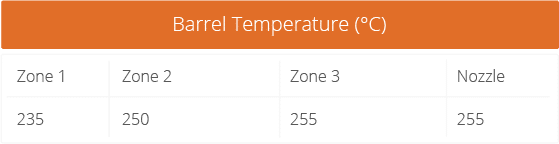
Flexdym Microfluidic Chips Replication
Sublym Machine vs. Hot Press
Essentially, Eden Tech’s mission is to create user-friendly microfabrication solutions to help researchers boost microfluidic chips production. Therefore, with the creation of Flexdym, it was important to offer an affordable machine to mold the material.
Notably, Flexdym’s thermoplastic properties mean it can be molded via hot embossing, just like other thermoplastics (e.g., COC, polystyrene, or polycarbonate). In essence, hot embossing involves utilizing pressure, heat, and time to transfer features from the mold to the material. Consequently, hot embossing is a great alternative to casting and soft-lithography methods of microfabrication.
Sublym Machine
- Optimized for Flexdym molding in only 1-2 minutes!
- Compact & User-friendly design that requires little to no training.
- Dramatically cheaper than most standard clean room equipment. This small investment is an opportunity for you to begin exploring microfluidics.
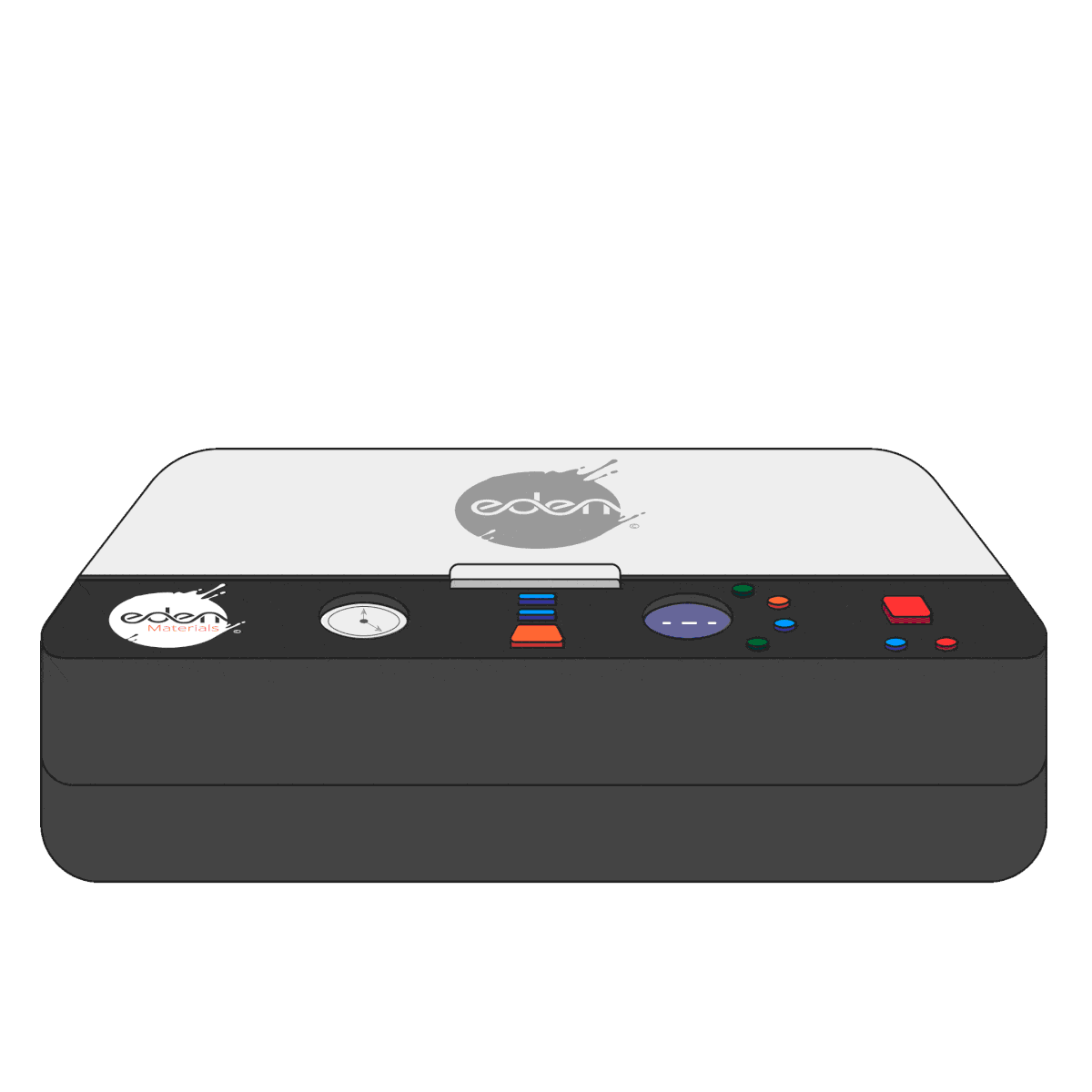
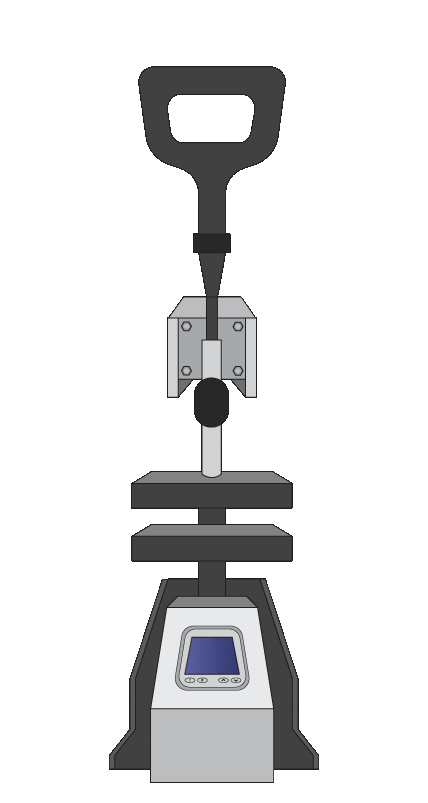
Classic Hot Press
- Not optimized for Flexdym molding, therefore longer molding time.
- Less easy-to-use alternative for the Sublym.
- Slightly more expensive than the Sublym100, but a standard piece of equipment which is generally installed in fabrication facilities.
Flexdym Pricing
Eden Tech has optimized Flexdym’s pricing to be comparable to other widely used materials in microfluidics, with added advantages:
- Biocompatible
- Transparent
- Scalable
- User-Friendly
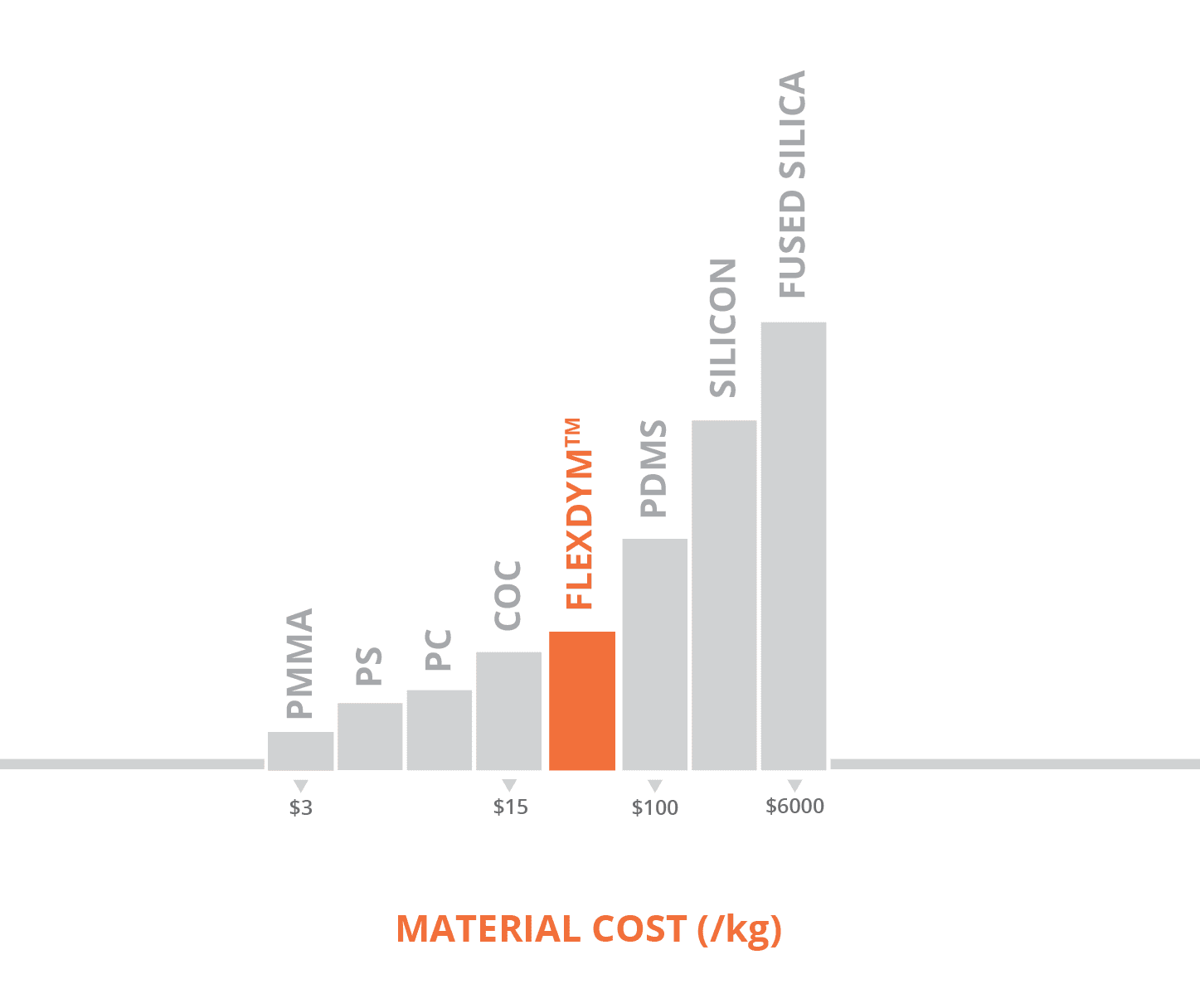
Gas Permeability of Flexdym
Specifically, we have conducted gas permeability tests for 2 mm of Flexdym at 23°C, 50% RH. Subsequently, these results, combined with those of other Flexdym users, show a range of 40 to 70-fold lower gas permeability for Flexdym compared to PDMS. Nevertheless, cell culture remains a top application of Flexdym. For instance, for published results, contact us.
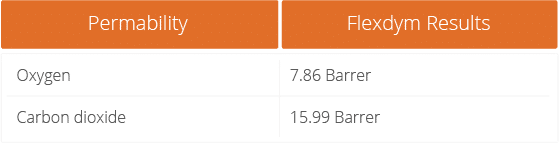
Resistance to Solvents
Much like PDMS and other thermoplastic materials used in microfluidic device fabrication, Flexdym™ is resistant to commonly used solvents such as acids and bases, as well as methanol/ethanol. Furthermore, it is resistant to fluorinated oils, commonly used in droplet-based microfluidic applications. However, like these other materials, results show it swells in the presence of carboxylic acid and other oils. Indeed, it may be important to note, it is not resistant to hydrocarbons. To that end, to find out more about Flexdym material chemistry, read our news article.
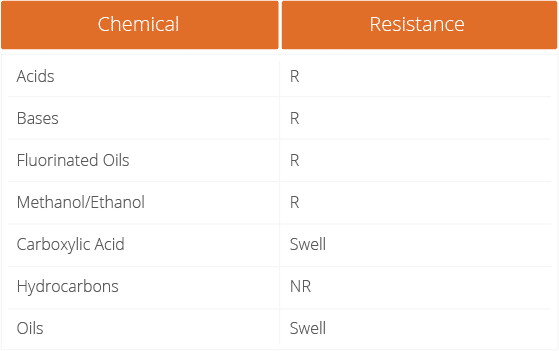
Top Flexdym Applications
- 2017 - Thermoplastic elastomer with advanced hydrophilization and bonding performances for rapid (30 s) and easy molding of microfluidic devices
- 2018 - Soft Thermoplastic Elastomer for Easy and Rapid Spin-Coating Fabrication of Microfluidic Devices with High Hydrophilization and Bonding Performances
- 2019 - Harnessing Nonlinearity and Asymmetry for Built-in Control in Mechanical and Fluid Systems
- 2019 - Microfluidics: Innovations in Materials and Their Fabrication and Functionalization
- 2019 - Development of fast and simple fabrication processes for paper-based microfluidics and alternative polymers to PDMS
- 2020 - Rapid Fabrication of Membrane-Integrated Thermoplastic Elastomer Microfluidic Devices
- 2021 - Facile engineering and interfacing of styrenic block copolymers devices for low-cost, multipurpose microfluidic applications
- 2021 - Estudi de la fabricació de canals microfluídics en làmines polimèriques i la seva unió mitjançant hot embossing i processos d’unió tèrmica
- 2022 - Complete fabrication station of scalable microfluidic devices for sensing applications
- 2022 - Engineering a sustainable future for point-of-care diagnostics and single-use microfluidic devices
- 2024 - Low-cost, versatile, and highly reproducible microfabrication pipeline to generate 3D-printed customised cell culture devices with complex designs
- 2017 - Insights on Polymers for Microfluidics Applied to Biomedical Applications
- 2018 - Desarrollo de sistemas microfluídicos en la multiescala para el cultivo celular y tisular
- 2019 - A methodology to develop a vascular geometry for in vitro cell culture using additive manufacturing
- 2021 - Cultivating Multidisciplinarity: Manufacturing and Sensing Challenges in Cultured Meat Production
Application Notes & Case Studies
Flexdym Mechanical Properties
Flexdym combines properties of thermoplastics and elastomers. This explains it’s elasticity (Young Modulus of 1.15 MPa) and simultaneous ability to be hot embossed.
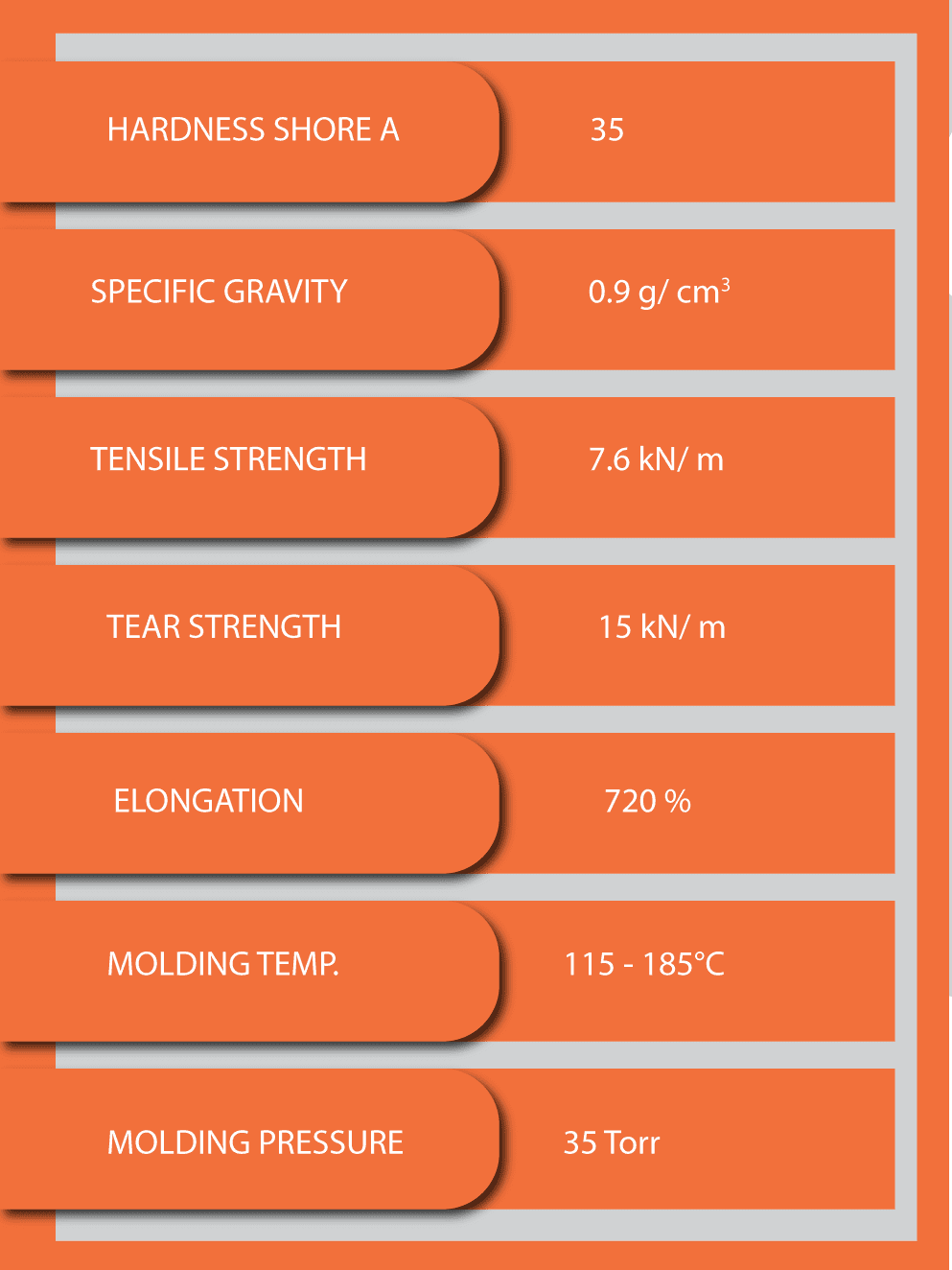
Flexdym For Diagnostic Devices
- Certified Biocompatible ISO 10993 parts 4, 5, 6, 10 & 11 AND USP Class VI.
- Optical transparency, with UV-Vis trasnmittance over 295-800 nm.
- Material cost optimization, ideal for POC cassettes & cartridges.
- Withstands thermocycling temperatures for PCR and others amplification reactions.
- Functionalization similar to other SEBS, via amino-based, EDC/NHS coupling & silane-based chemistry.
- Resistant to fluorinated oils, ethanol, acids & bases.
Flexdym for Cell Study Devices
- Certified Biocompatible ISO 10993 parts 4, 5, 6, 10 & 11 AND USP Class VI.
- Good cell adhesion & proliferation over long time periods.
- Bonding to PS, glass and other commonly used cell culture materials.
- Good bonding strength up to several bars, withstands 37°C humidity conditions.
- Stable hydrophilicity post plasma treatment.
- Gas permeable, but low sorption of small molecules.